microMIG-cc Process:
Mechanical droplet detachment without intermediate pulses
The rapid succession of forward feed and retraction of the wire electrode creates an interplay of arc phases (red) and short circuits (blue).
The relatively high, constant welding current generates enough heat during the arc burning time (red) to melt the base material and produce a molten droplet at the end of the wire. Due to the significantly reduced energy within a subsequent short-circuit phase (blue), the weld pool can cool down and heat can be dissipated into adjacent base material areas.
An arc burns between the forward-fed wire electrode and the workpiece. The effect of the constant welding current heats up the workpiece and the filler material. During the arc burning period, a molten droplet is formed at the end of the wire. As soon as the wire touches the weld pool, a short circuit occurs and the arc goes out. By pulling back the wire, the droplet is mechanically detached and the short circuit is canceled again. The arc ignites again and a new heating phase begins. The wire electrode is retracted to the set distance from the weld pool. The process begins to repeat by feeding the filler material forward again.
Special features – microMIG-cc
- heat-reduced welding process
- better control of the heat input into the workpiece
- less workpiece distortion
- welding with low spatter and uniform penetration
- clean welding process – reduces maintenance efforts
- excellent gap bridging
- wider welds – larger process window in case of misalignment
- welding speed comparable with standard MIG/MAG processes
- very appealing weld appearance
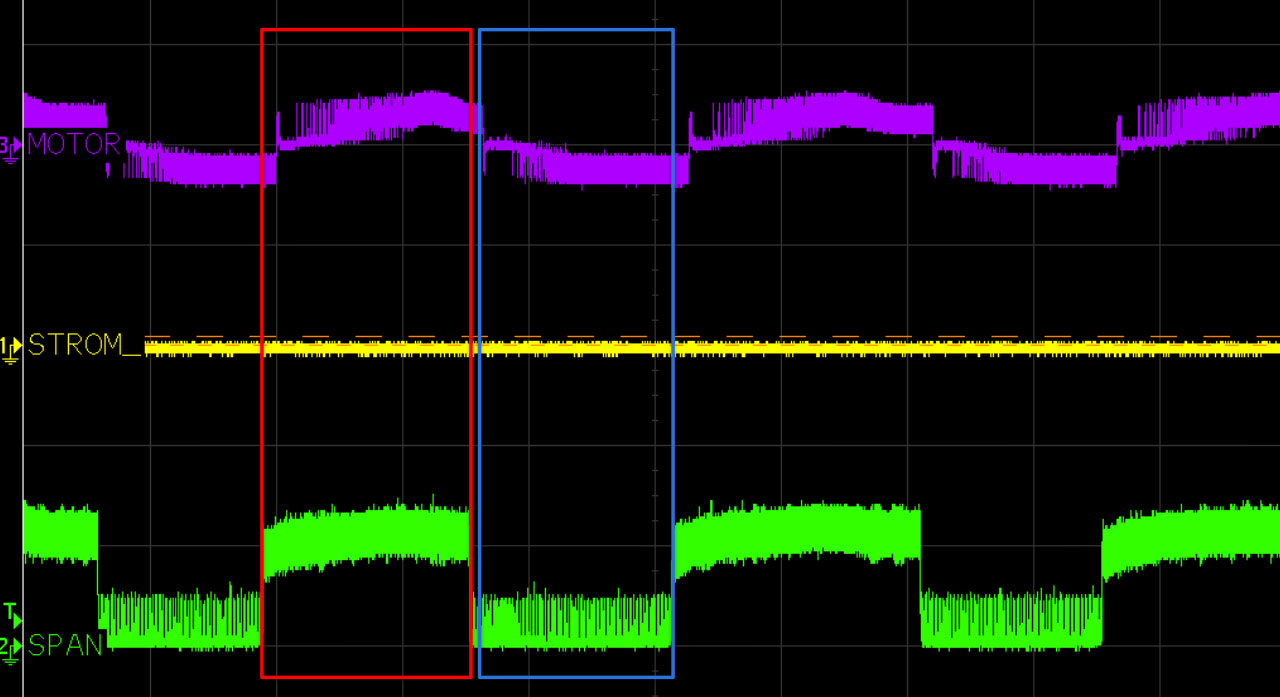
Video: microMIG-cc welding process
Video: microMIG-cc welding process
SKS Weld Packages
This might also interest you
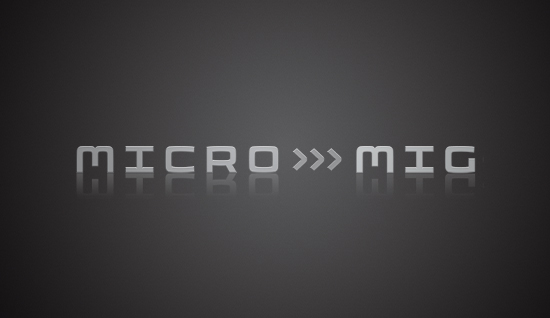
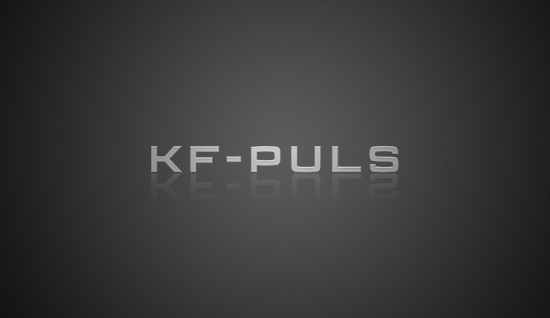
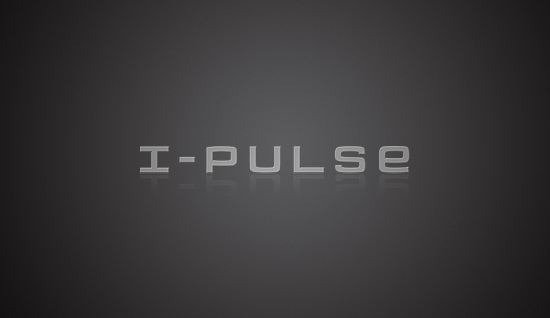
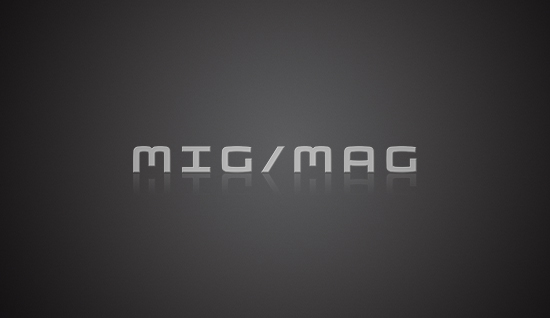