SKS Monitoring Functions
The SKS welding system includes integrated monitoring functions for quality assurance in ongoing production and to support optimization and troubleshooting. These allow to detect irregularities and deviations of the most important process parameters during the welding process and to actively interrupt the welding process or send corresponding alarm messages to the system control if predefined limit values are exceeded or not reached.
Especially in interlinked production lines, this can significantly reduce the costs of rework or rejects, since deviations can be detected more quickly and defective workpieces can be removed from the line for possible repair. Due to the output of more than 100 different error codes with plain text display, error causes can be determined very quickly and expensive downtimes can be significantly reduced.
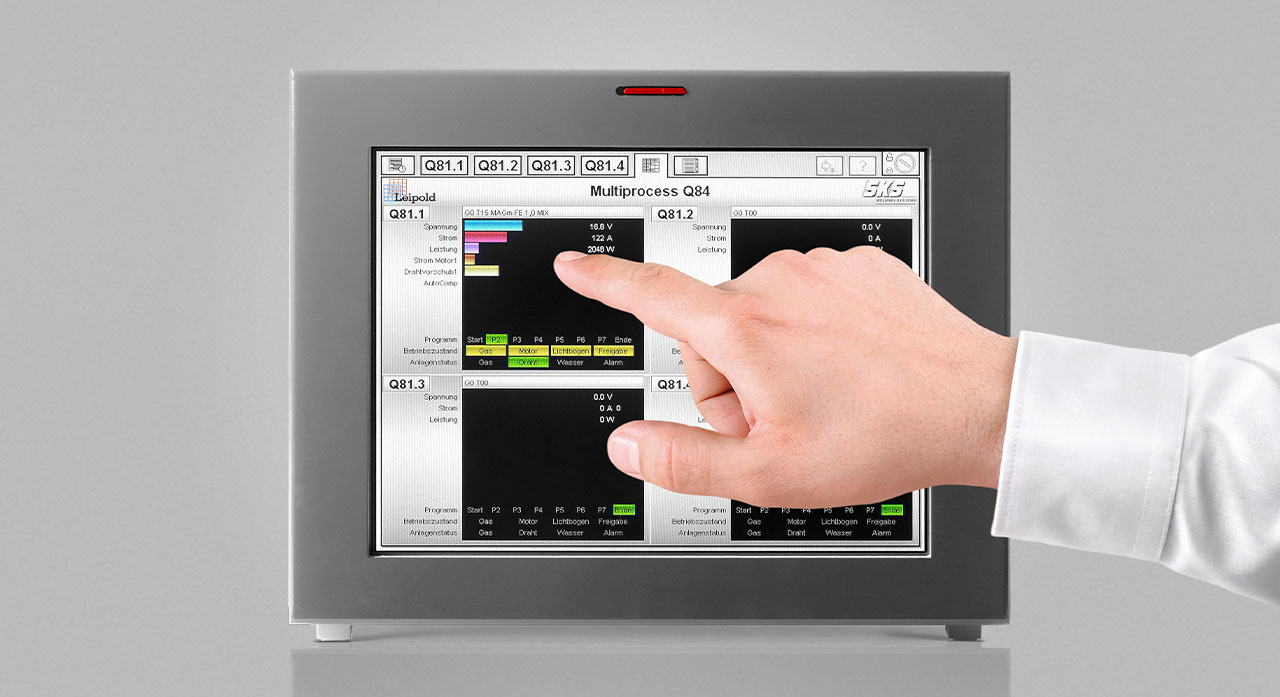
Monitoring functions
Software
AutoCheck
- Hardware self-diagnosis to check for errors of the connected components and their configurations
- Alarm output for faulty components
Arc sensors
- Monitoring of the measured electrical parameters
- Welding process can be actively interrupted in case of overshoot or undershoot
Ignition Filter
- after receiving the arc start signal(from Robot or PLC), arc have to be established within a programmable filter time
Start-Filter (arc start monitoring)
- After receiving the start signal (from robot or PLC) the arc must be ignited within a programmable time
Libo-Filter (arc monitoring)
- Minimum values for current and voltage are monitored to detect an existing arc
Current window (welding current monitoring)
- Monitors the average welding current per weld
- Very fast indicator for changes during welding (wire feed issues, torch distance, ...)
Energy window (option when using Synchroweld)
- Expansion of welding current monitoring to include the current robot speed
- The welding controller calculates and monitors predefined values of the heat input per unit length
AutoCOMP (welding voltage monitoring & resistance compensation)
- Monitors the welding voltage and reacts actively to changes in the electrical resistance in the welding circuit
- Indicator for the detection of cable breaks, shunts or damaged insulation
Motor Current Monitoring
- The set and actual values of the motor current are displayed and monitored on the weld process controller
- Higher or increasing values indicate problems on the wire feeding line (damaged or contaminated wire cores); exceeding the set values will trigger an alarm at the end of the weld seam
- Very useful for preventive maintenance
- Can significantly reduce downtime
Advantages – Monitoring functions
- Active reaction: due to the integration into the welding system, reactions to alarm messages can be carried out directly by the welding device; alarm messages can lead to the shutdown of the welding process or only be displayed
- No additional costs: included in standard scope of delivery
- No additional cabling: installed within the components
- No additional interface to the robot required: communication takes place via the interface of the welding system
- No additional data backups: settings are saved in the controller backup
- Integrated monitoring sensors: all monitoring is managed within the welding system and parameterized or displayed via the welding controller
Hardware sensors
- Detection of insufficient shielding gas quantity or cooling water flow, end of the filler material
- Welding can be actively interrupted in case of missing media or welding wire
Shielding gas monitoring
- Integrated gas flow sensor
- Monitors the shielding gas quantity in l/min
- Setpoint and actual values are displayed on weld process controller
- Gas pressure switch
- Monitors ring line pressure (min./max. value)
Water flow monitoring
- by means of a system-integrated water flow sensor
- Monitors the water flow rate in water-cooled torch systems
Wire end sensor
- Integrated wire end sensor
- Monitors availability of the filler material
Ferrite sensor (for exhaust gas system production)
- Differentiation between ferritic and austenitic filler materials
This might also interest you
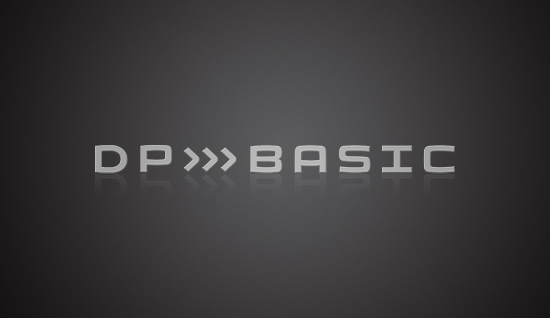
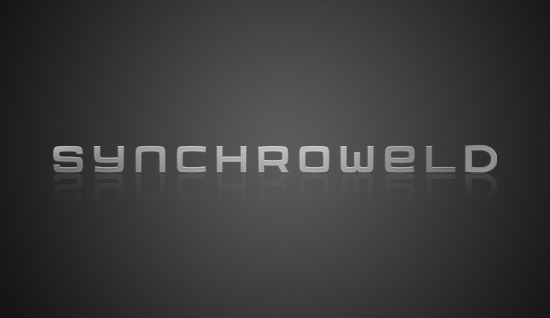
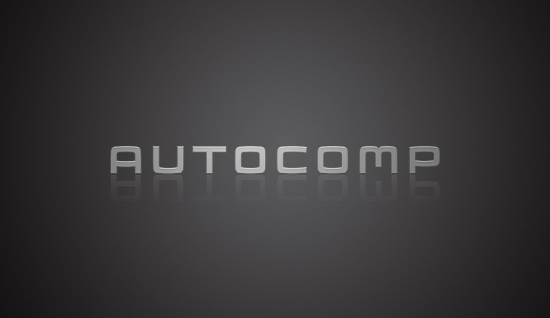
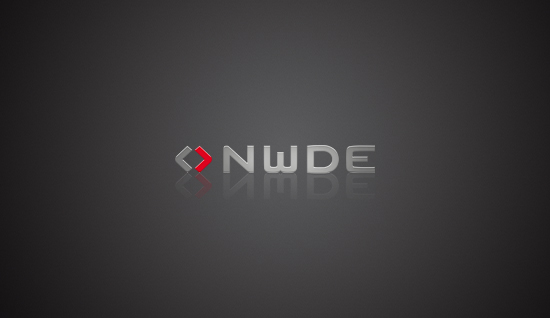