KF-pulse Process:
Special pulsed process with integrated short circuit routine
Standard pulse processes control only one value at a time (I or U); the second value is not limited and upwardly open. Short circuit events make the process choppy and usually result in weld spatter. The KF-pulse method limits both settings, max. current and max. voltage, and thus creates a characteristic map. This limits the maximum energy per pulse and the heat input into the workpiece can be effectively controlled and limited. Each pulse heats the base material and creates a single droplet which is formed at the end of the wire, detached and transferred to the molten weld pool. During the base current time, the material cools down and the wire is brought closer to the weld pool. A special short-circuit routine significantly reduces spattering and enables a very short, powerful arc to be set. The very short arc length reduces heat input into the workpiece, increases gap bridging and enables welding in constrained positions.
Special features – KF-pulse process
- very short, powerful arc
- reduced heat input per unit length (-8 to -10%)
- little spatter
- consistent, reproducible penetration
- good gap bridging
- suitable for constrained positions
- avoidance of undercuts
- can be used with all SKS Weld Packages
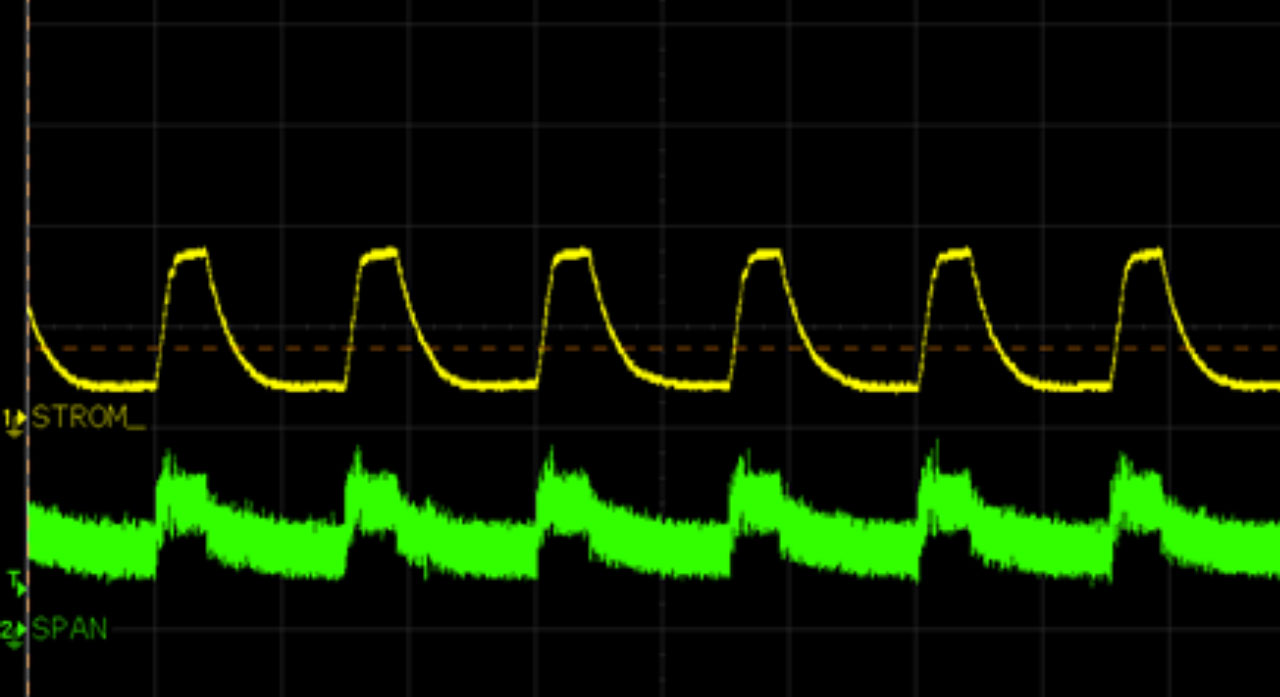
Highspeed video: SKS KF-pulse welding process
SKS KF-pulse welding: Welding of the fillet weld begins in the overhead position. During welding, the table moves to the inclined position. No parameter adjustment during the entire welding process.
Video: fillet weld with SKS KF-pulse process
Video SKS KF-pulse welding process (0.8 mm overlap seam)
This might also interest you
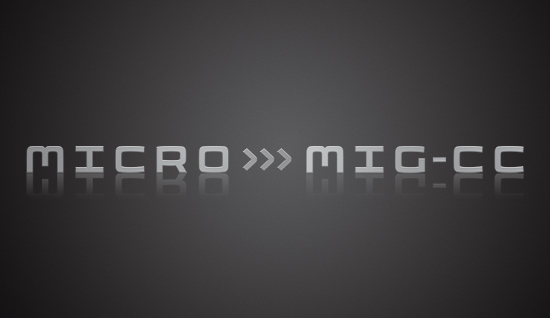
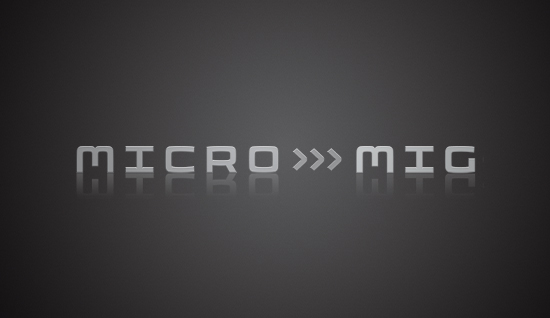
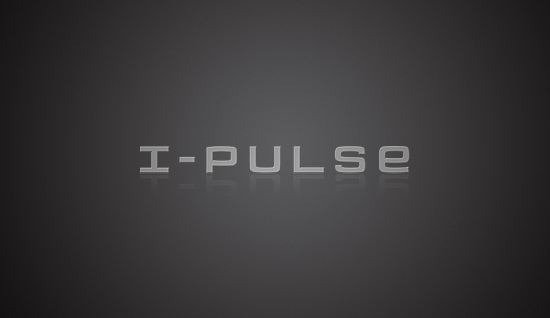
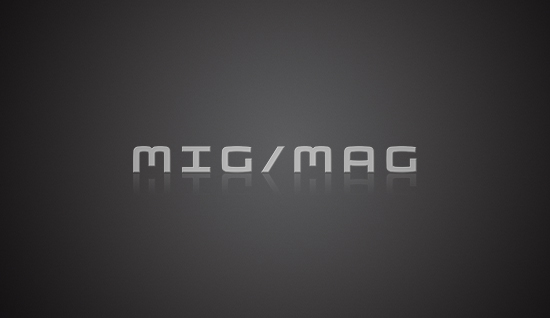