Efficient cleaning of gas nozzles with eReam 2.0
In automated arc welding, torch cleaning affects both the cost and productivity of the whole process. To positively influence both factors, the eReam 2.0 innovative torch cleaning system offers striking benefits.
Its all-electric drive saves considerable amounts of energy compared to pneumatic drives, is easier to control, complies with the applicable safety regulations and offers good monitoring capabilities. Cleaning with reaming blades proved as the best solution from the point of costs, reliability and manageability. The decision to use electric motors rather than pneumatic systems opened various possibilities concerning control and sensor technology. Thus, the cleaning process runs automatically programmed.
Learn more about our Reamer Blades
Downloads
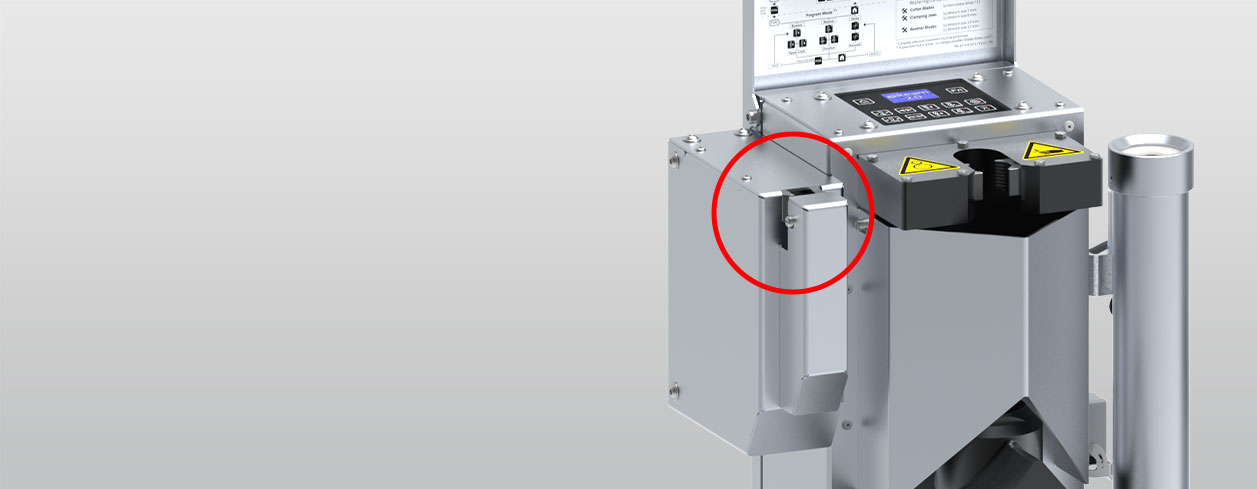
- Exact cutting through motor driven cutter-blades
- All cutter-blades are multi-side sharpened
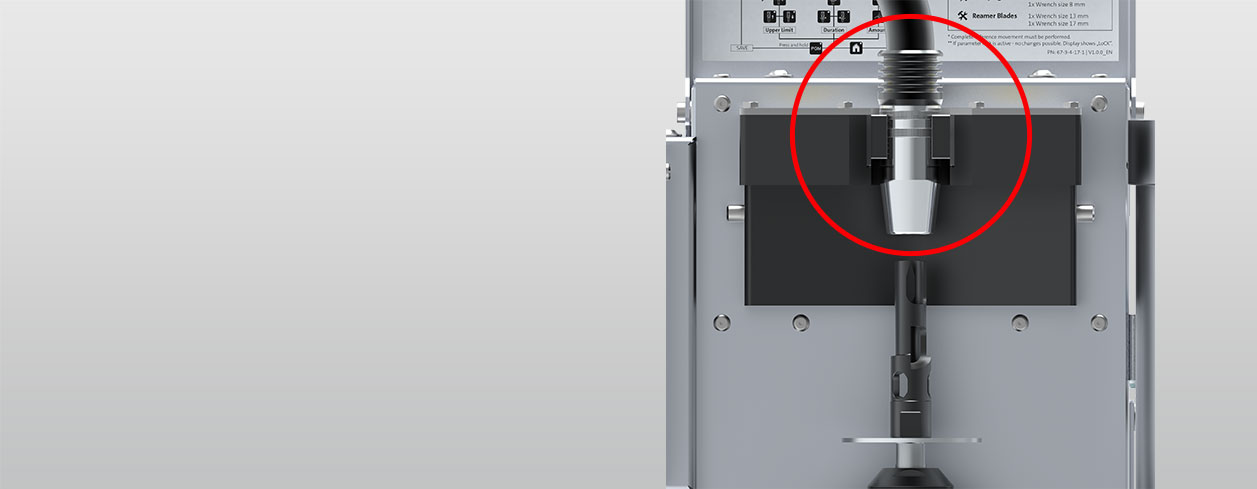
- Force controlled and centered clamping of gas nozzle
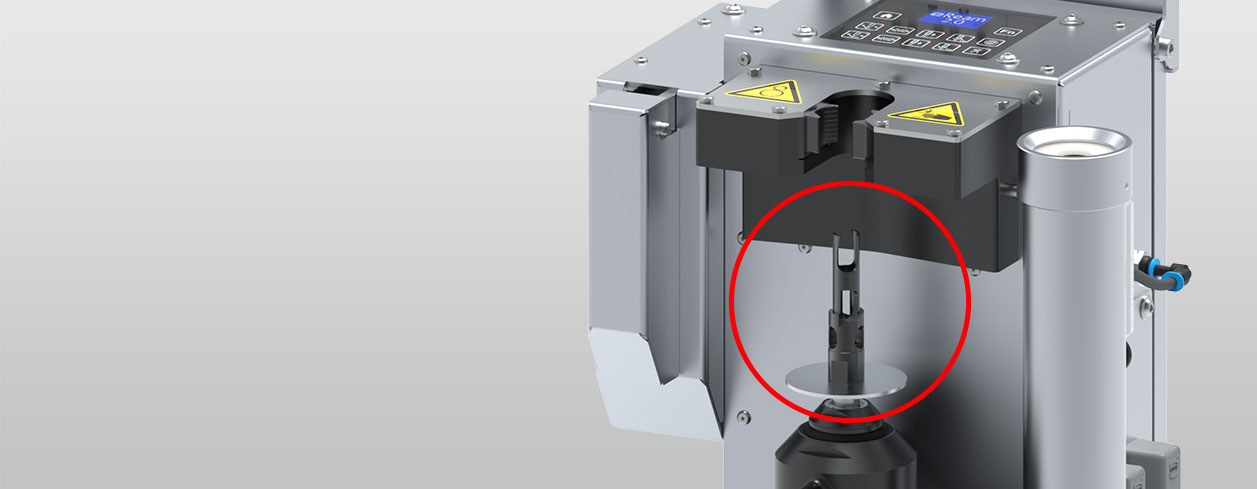
- Precise stroke length (protection of consumables)
- Way and force supervision of cleaning process (damage prevention)
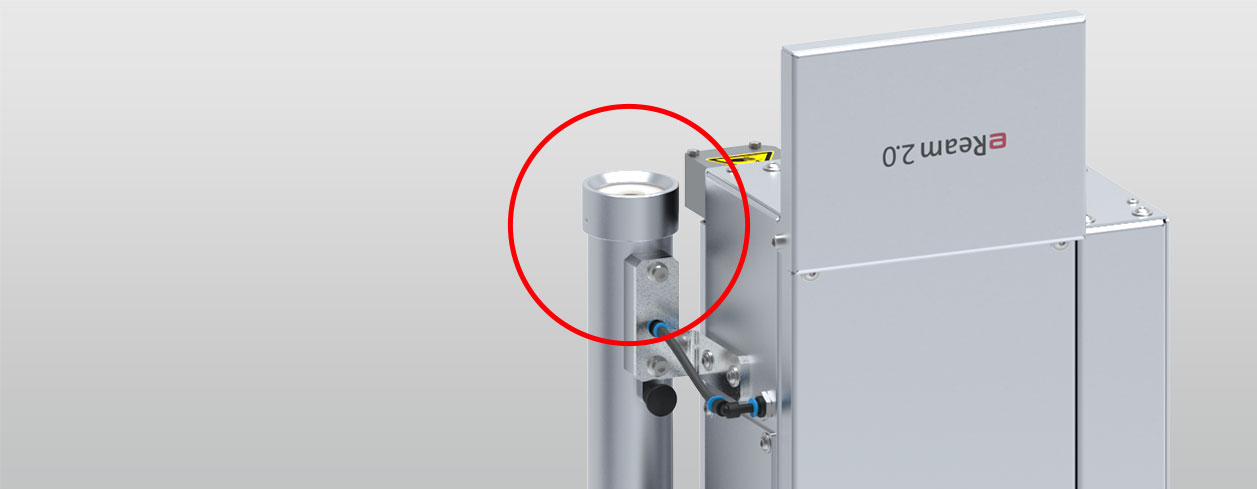
- Pulse-triggered spray (exact amount of anti-spatter spray)
- Full/Empty indication of anti-spatter liquid
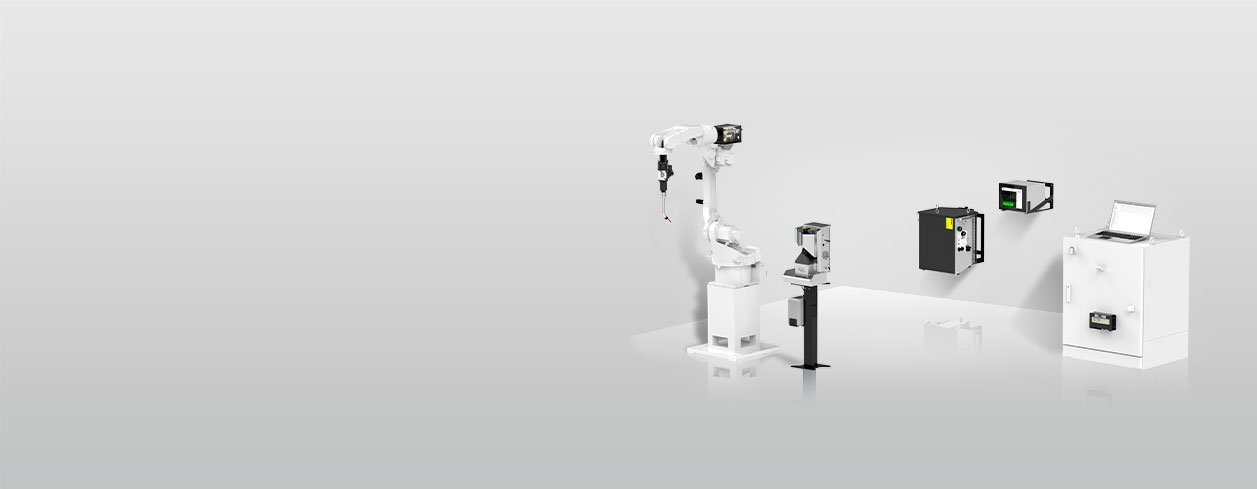
- Display shows status information (directly at the unit or via digital I/O)
- Easy usage (simple menu navigation)
- Full integration into safety circuit
- Manual Mode (Setup mode with minimum speed of all motors)
- User access control
Technical specifications
- Dimensions (H x W x D in mm): 410 x 278 x 280 (without wire cutter) / 410 x 337 x 280 (including wire cutter)
- Weight (in kg): 14,3 (without wire cutter) / 17,0 (including wire cutter)
- Cycle time without wire cutting (in sec.): ~ 6
- Cycle Time wire cutting (in sec.): ~ 1
- Dimension of mounting holes (W x D in mm): 120 x 220 (4x M6)
- Max. possible gas-nozzle outer diameter (in mm): ≤ 34
- Max. possible wire diameter (in mm): ≤ 1,6
- Compatible anti-spatter fluid: request data sheet from SKS
- Feeding of anti-spatter fluid: External (self-priming)
- Performance level: PLd C (under test)
Energy
- Power supply: External (power supply cable)
- Nominal voltage: 24 VDC (+10% / - 5%)
- Rated current: 5 A
- Nominal power: 120 W
Connections on back side
Connections on back side
- Plug 10-pol Harting HAN High Density (X1): Control cable digital I/Os
- Plug 5-pol Harting HAN 3A (X2): Power supply