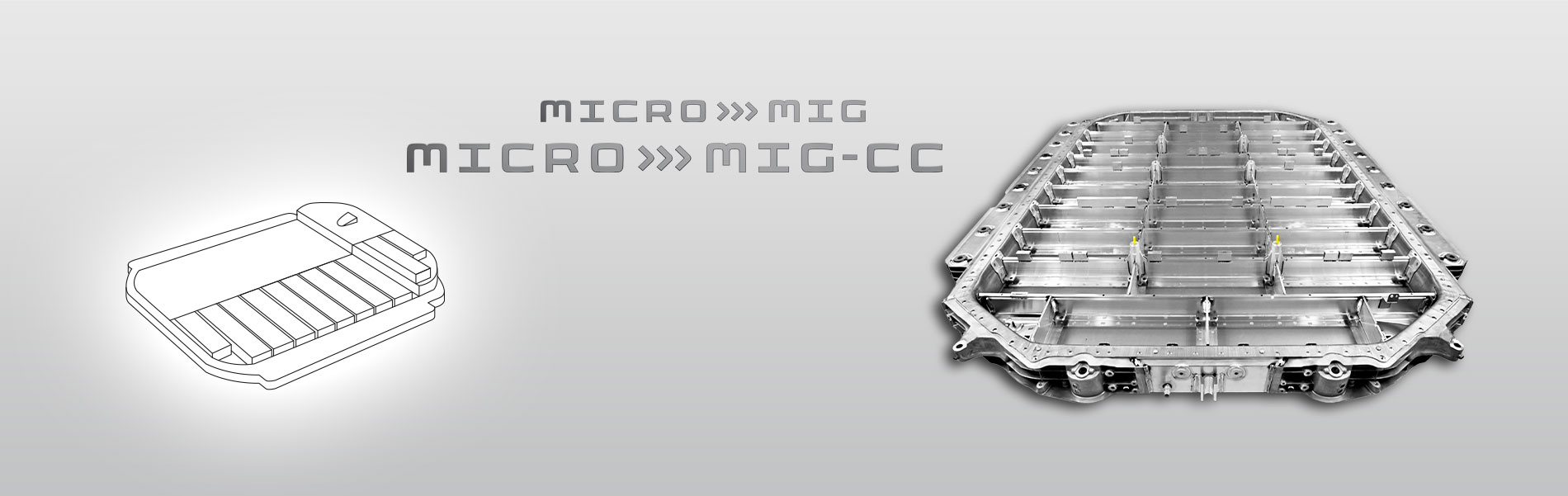
Battery Tray Systems
Battery tray systems are a relatively new field of application in automotive engineering, which is growing very rapidly due to the worldwide promotion of e-mobility. SKS recognized this trend early on and developed solutions for the required joining tasks in cooperation with automobile manufacturers already in the prototype phase.
The entire assembly of a battery carrier system is subject to high tightness requirements to reliably prevent the ingress or escape of media. In this context, the absolutely reliable reproducibility of welded joints is of prime importance to the manufacturers.
Today, the battery carriers of the first mass-produced electric vehicles on the road are welded with SKS welding systems.
Welding challenges
- different base materials
- coated surfaces
- relatively large components
- tightness requirements
- (special) cleanliness requirements
- air gaps
- weld offset due to component distortion
- dirty / oily surfaces
Prerequisites
- optimized / close-to-process wire feeding
- precise heat control / heat-reduced welding processes
- reproducible welding processes / welding parameters
Application – Battery Tray Systems:
Galvanized Steel
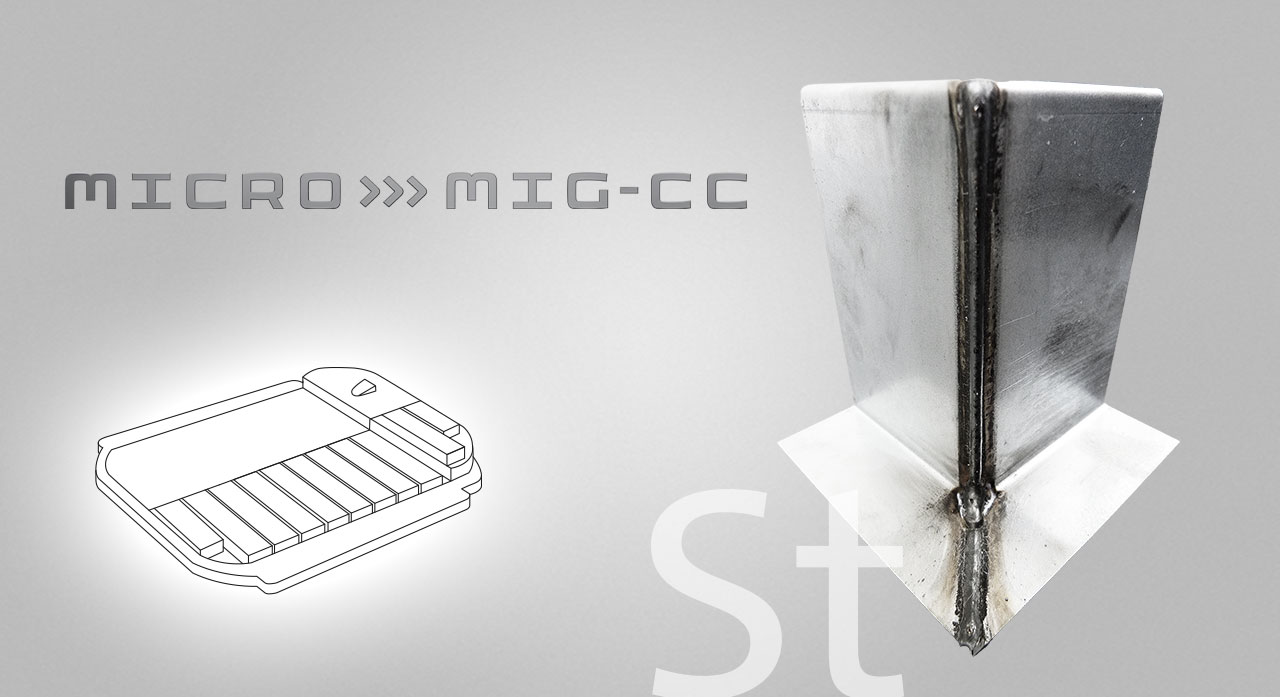
The battery tray, i.e. the actual container for the battery cells, is subject to very high tightness requirements and must remain stable for the entire life cycle of this component. Because of its good corrosion properties and low cost, these components are therefore made, for example, of galvanized sheet steel. In order to meet the high requirements, specially coordinated joining processes are needed so that problems such as pore formation due to zinc outgassing can be effectively suppressed.
Application – Battery Tray Systems:
Aluminum
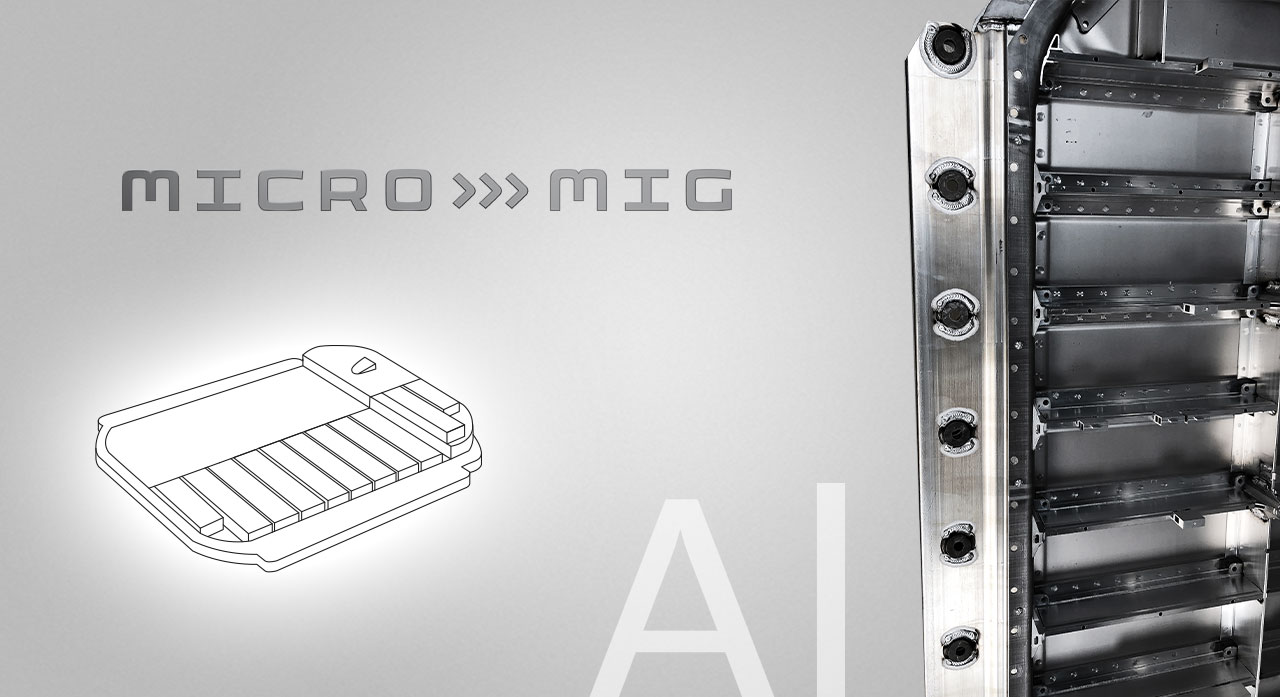
For reasons of weight, battery carrier systems are often made of aluminum. The so-called “crash frame” is welded together from extruded aluminum profiles, sometimes in combination with cast and sheet metal parts. The battery trays of the next vehicle generation take up the entire underbody as installation space. The increased processing criteria and the size of these components present manufacturers with new challenges. The SKS welding system supports users in this task with optimized welding equipment, welding processes – and extensive experience from previous projects.