
Chassis
With its Power Joint torch system and the KF-pulse process, SKS has been setting the benchmark for welding automotive chassis parts for years.
The manufacturers of these highly dynamically loaded vehicle components are mainly concerned with the largest possible and stable process window and maximum availability of the welding system. SKS meets these requirements with the required know-how and precision.
Welding challenges
- different materials (steel, high-strength steel, galvanized steel, aluminum)
- coated surfaces (different coating types and thicknesses)
- high welding speed
- air gaps
- weld offset
- long welds
- risk of cracks
- risk of pores
Prerequisites
- correct selection of the welding process
- precise thermal control
- reproducible welding parameters
- stable arc ignition
- good gap bridging
- good weld pool control
Application – Chassis:
Steel
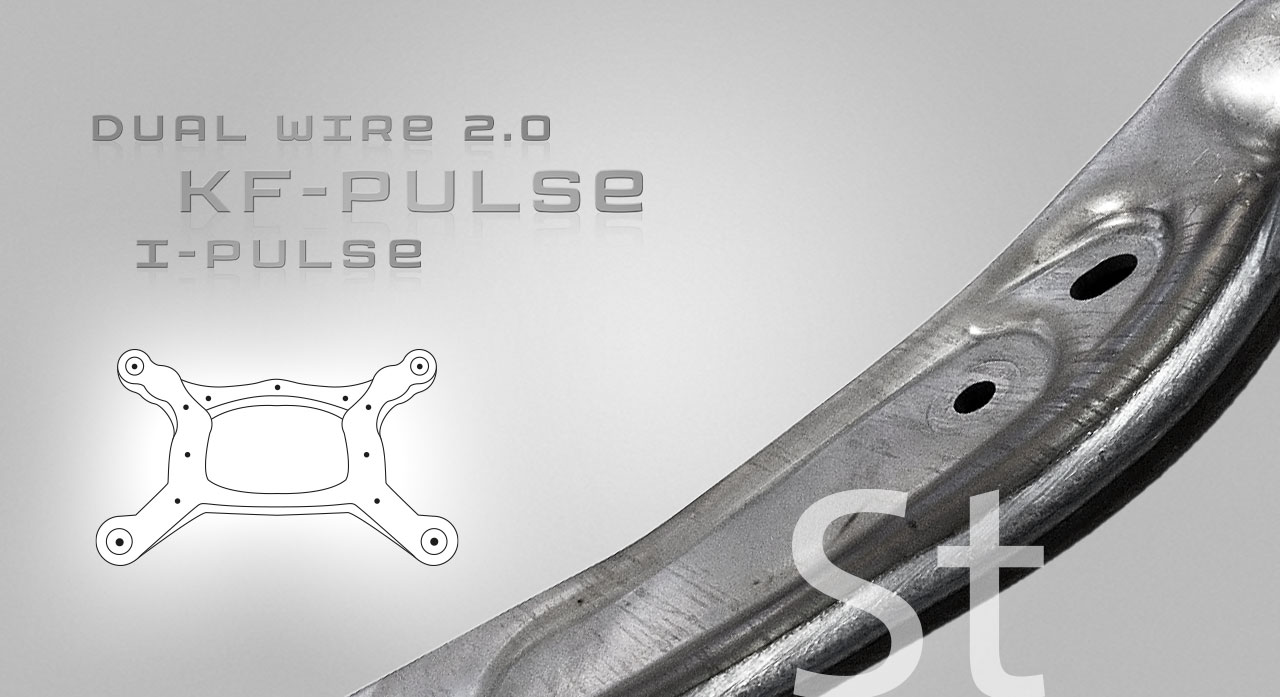
In addition to high joining speeds, good gap bridging and tolerance against weld offset, the use of high-strength steels in axle applications often also depends on correct heat conduction to prevent, for instance, the development of cracks. The KF-Pulse process, which is frequently used in the steel processing industry, ensures very clean, low-silica weld surfaces in combination with argon-rich inert gases. The very short, powerful arc ensures repeatable welding results and high welding speeds.
Application – Chassis:
Steel, double wire
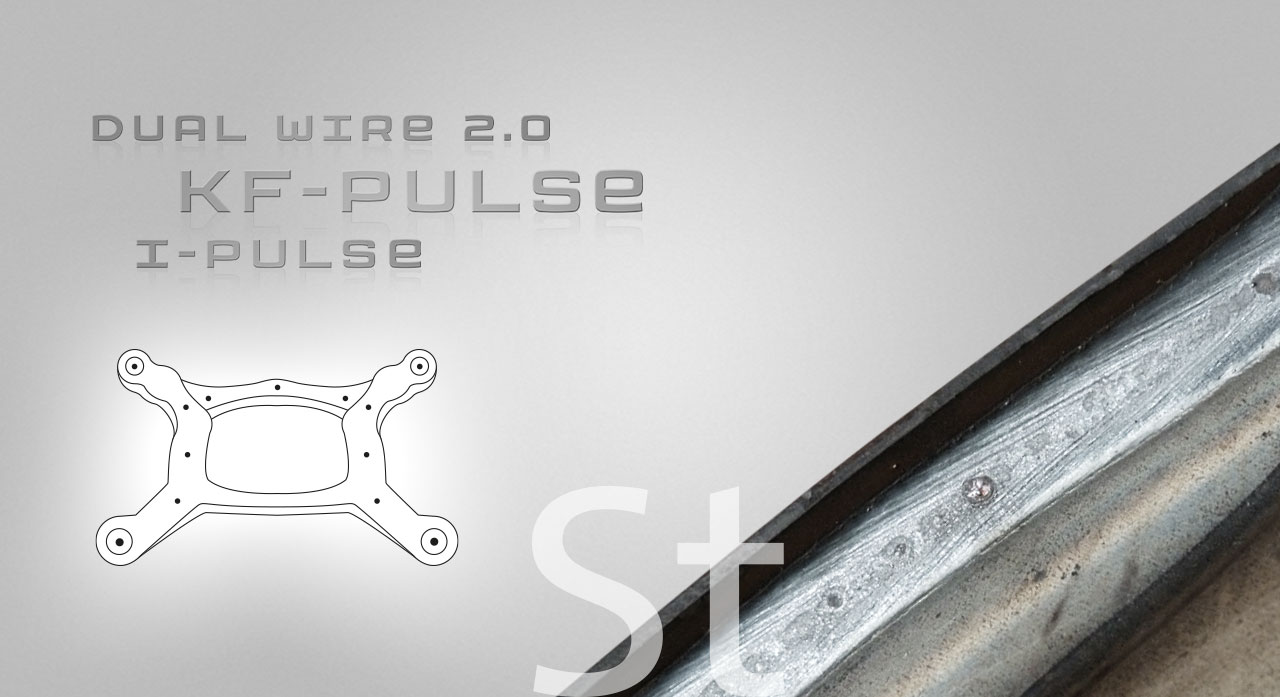
In order to increase productivity, more and more efforts are being made today to minimize process times. One way to achieve this is the use of fully mechanized MSG multi-wire welding processes. By using the SKS Dual Wire, the welding speed can often be doubled compared to single wire applications. With material thicknesses from 2 mm and especially with longer weld seams, you can get the full benefit of th higher welding speed. The compact design of the dual-wire torch system allows good access to the welding device. The parallel arrangement of the two welding wires simplifies the programming of the robot, especially for highly contoured workpieces.
Application – Chassis:
Galvanized Steel
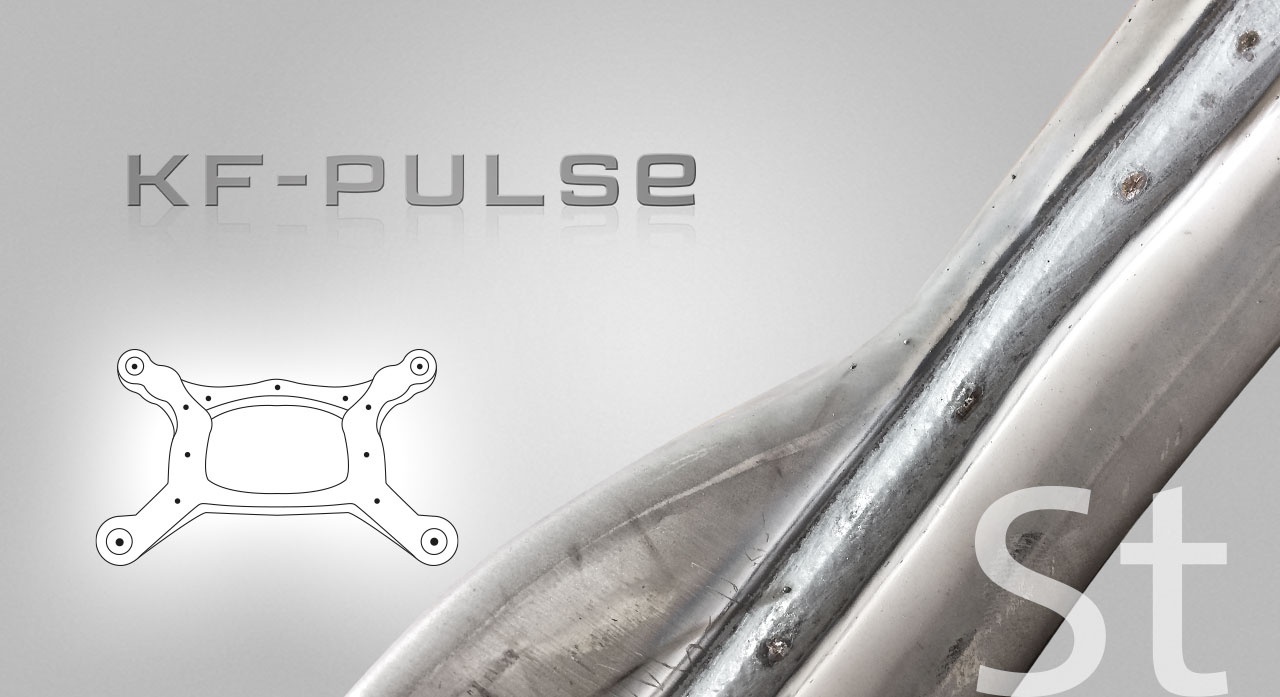
With the increasing reduction of material thicknesses, corrosion protection is coming more and more into focus. For this reason, coated base materials are being used more and more frequently. However, the galvanized surfaces, which provide effective protection against perforation by rusting, usually have a rather negative effect on arc welding. Thus, the formation of pores and weld spatter must be avoided or minimized by suitable welding processes and weld seam preparation. The very short arc of the KF-Pulse process very often provides the decisive advantage here. Due to the smaller arc area, less coating is burned off and pore formation is significantly reduced.
Application – Chassis:
Aluminum
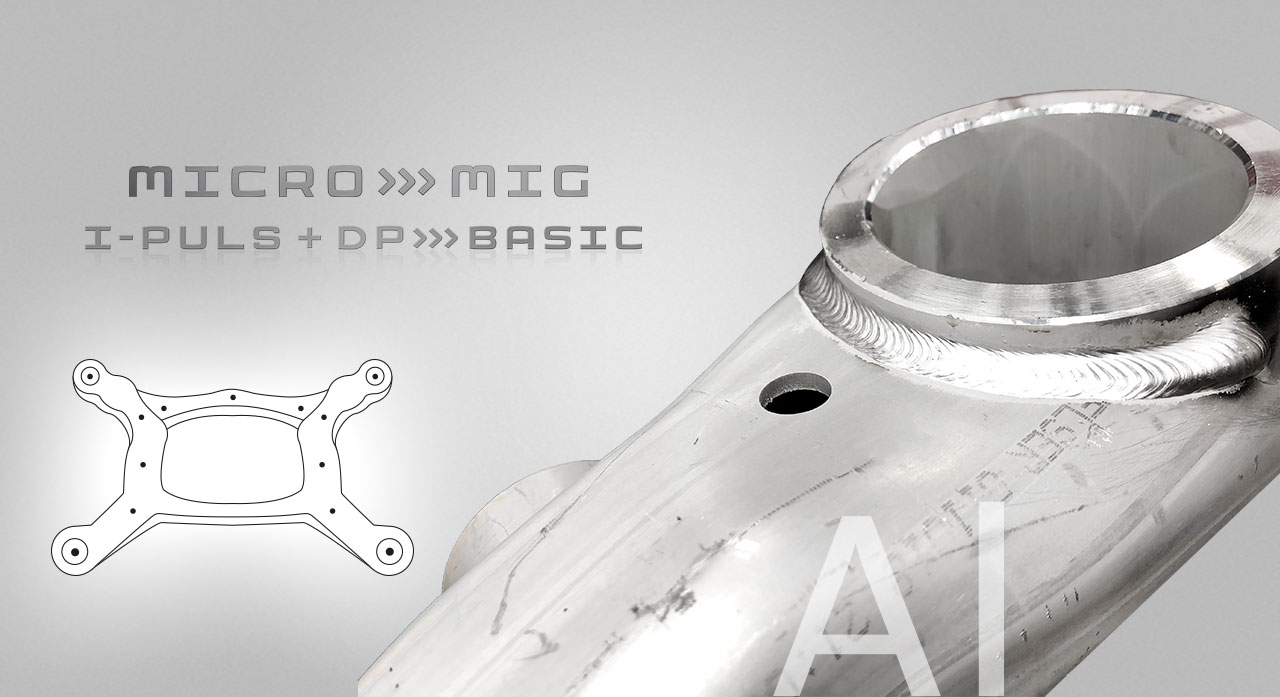
Advantages in driving behavior and lower energy consumption are often the reason for using the lightweight material aluminum in automotive chassis construction. The special properties of the alloys used increase the demands on the joining methods and processing techniques used.
The combination of castings, extruded profiles and sheet metal parts results in torsionally stiff and lightweight components for executive cars. Excellent seam appearance additionally underlines the high-tech character of these structures.