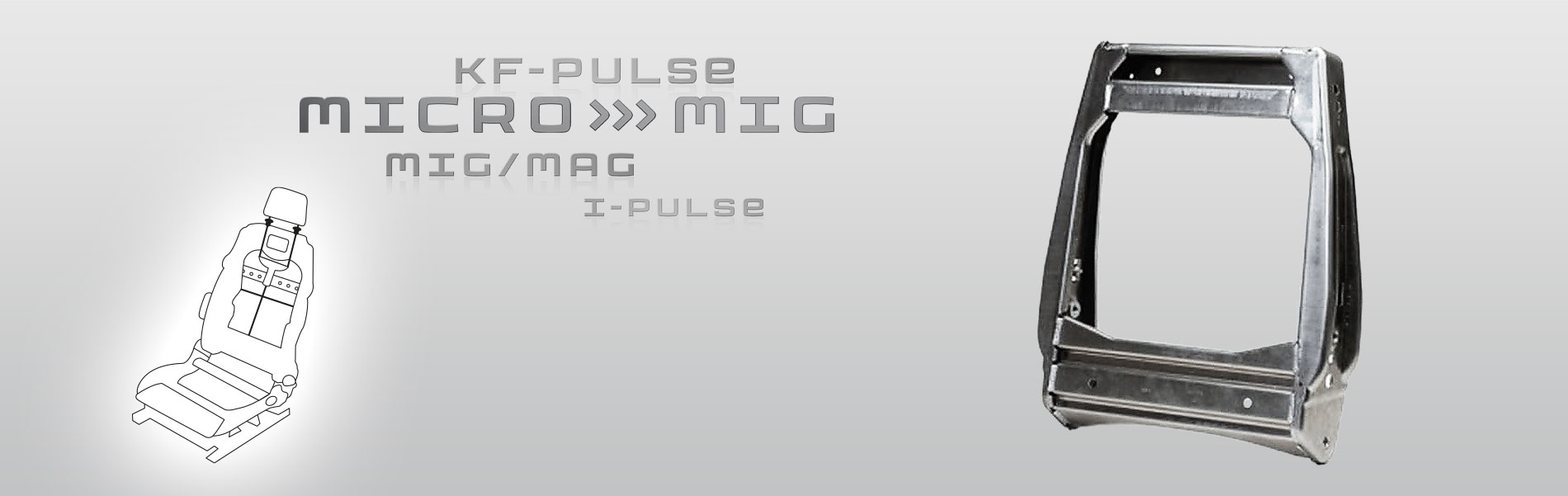
Seats
Since the company was founded over 30 years ago, SKS has been involved in the welding of car seat parts. Together with global seat manufacturers and suppliers, we constantly developed future-oriented solutions to meet the increasing lightweight construction requirements of the vehicle manufacturers.
For example, SKS has developed special processes for root welds to save the costs of weld preparation and to significantly increase process reliability.
Welding challenges
- very thin molded parts
- joining thin sheets with thicker hardened parts
- short welds – many arc ignitions
- air gaps
- weld offset
- dirty / oily surfaces
Prerequisites
- optimized / close-to-process wire feeding
- precise heat control / heat-reduced welding processes
- reproducible welding processes / welding parameters
Application – Seats:
Steel
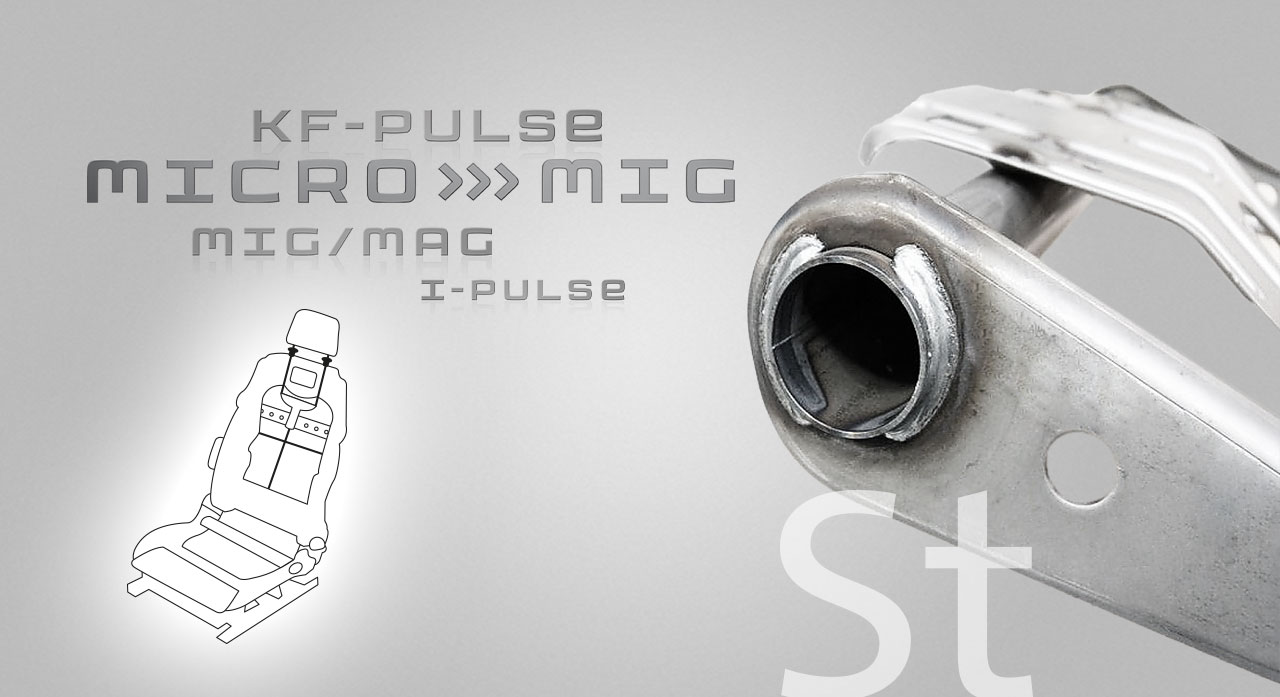
The thin-walled steel molded parts for backrest and seat structures are usually joined together with only short weld seams. In the event of a crash, however, the joints must meet extremely high strength requirements in order to protect the vehicle's passengers from injury. Solid hardened steel backrest recliners provide the connection between the backrest and the bottom part of the seat and also serve to adjust the inclination. They increase the difficulty of the joining task due to the special properties of the base material and the connection to the significantly thinner sheet thicknesses of the backrest and seat frames.