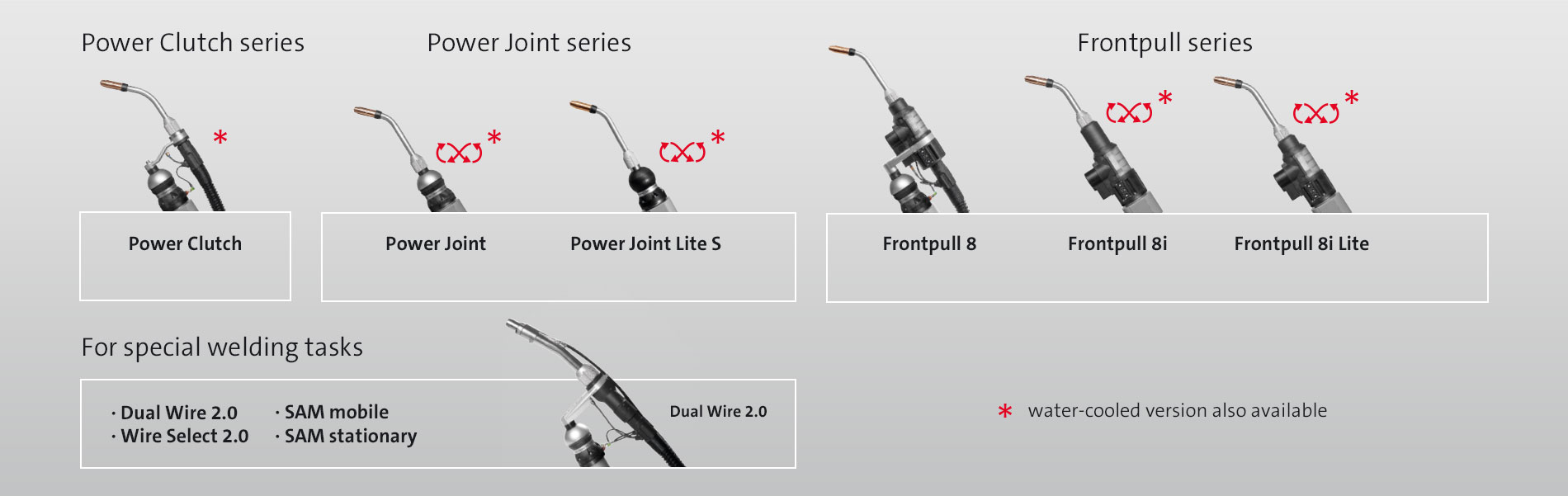
The innovative torch series for your welding tasks
Overview SKS torch series
With the introduction of the air-cooled robot welding torch in Germany of SKS Welding Systems offered the users considerable optimization potential. Air instead of water – a little revolution – means: no hoses, no leaks, no damage through leaking moisture, no excessive components. This success motivated us to create a torch series, in which we transferred the air-cooling principle to the single wire torches of our product line.
The results are compelling: From the air-cooled Power Joint with internal welding cable and limitless torch rotation (even beyond 360° without stop) up to our latest development – Frontpull series for heat and spatter-reduced welding. Our torch systems are compatible with all common welding robots.
With the modular design of our torch series, we enable our customers to use them flexibly in a wide range of applications. All SKS torch necks can be used, for example, incombination with the various SKS torch systems, as well as all SKS wear parts. The torch cables of the external SKS torch systems fit all torches in the series – including the water-cooled torch models.
Frontpull series:
For heat- and spatter-reduced welding with perfect penetration
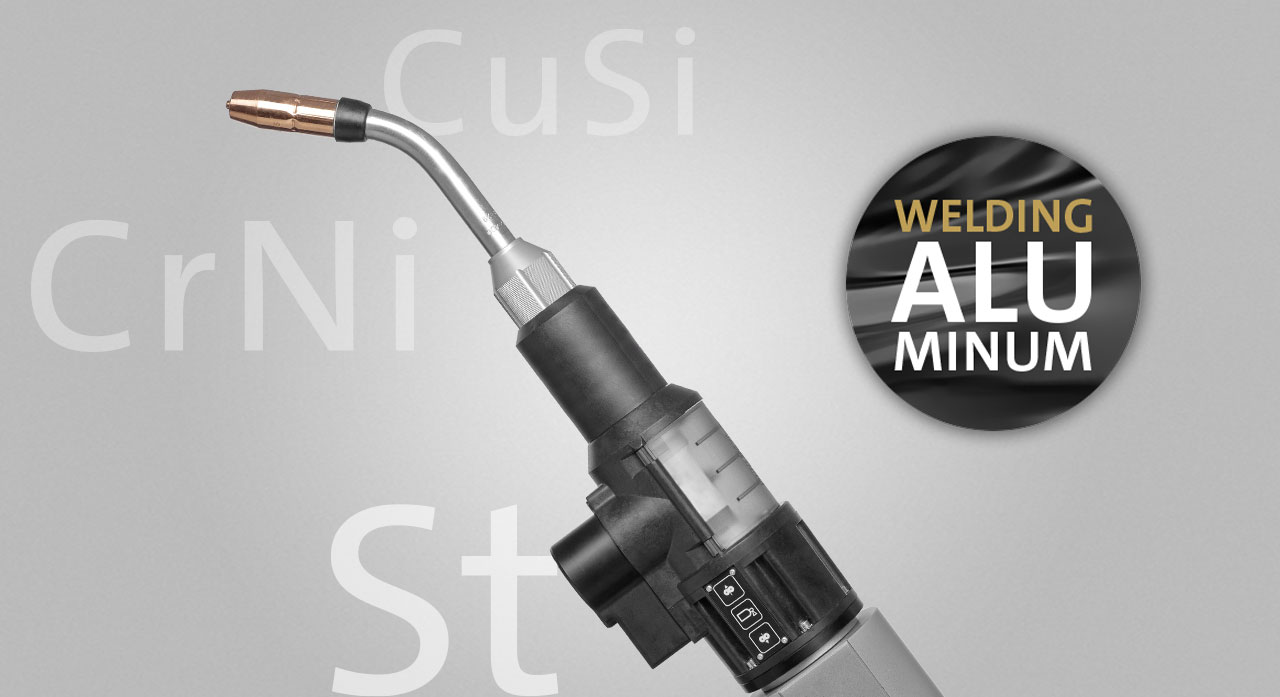
With the torch systems of the Frontpull series, SKS offers an alternative solution for conventional push-pull systems. The Frontpull series combines the wire feeder and torch to a single system. The result: a high-performance, high-precision wire feeder close to the process with an extended range of applications and processes. The torch systems equipped with two fully synchronized wire feed units expand the application options to include the microMIG process with reversing wire movement. Synchronization issues between the torch and the front pull module mounted on the robot arm are eliminated by design. The improved wire feeder supports spatter-reduced arc ignition (LiftARC) and ensures a safe and uniform wire feed even with very soft aluminum filler materials.
The Frontpull series offers torches for standard or hollow shaft robots, as well as air- or water-cooled versions. Thus, the torches of the Frontpull series can be used in almost any application area.
Power Joint series:
Our original for endless rotation
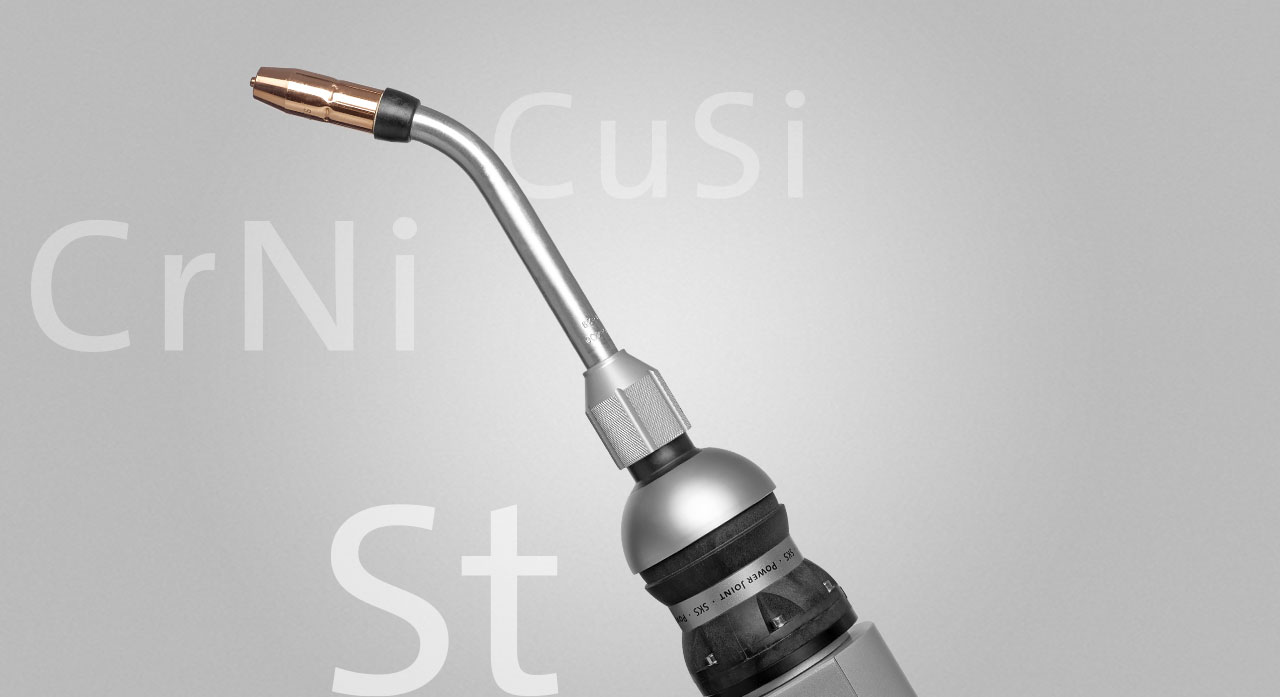
With the development of the Power Joint, SKS set a new industry standard. From the first ideas to the conceptual clarity of the implementation to the mechanical precision of the details, the Power Joint welding torch system is a special engineering achievement – and the first of its kind. Meanwhile, over 15,000 Power Joints are successfully operating under industrial conditions worldwide. The high acceptance among SKS’ customers and the constantly growing demands of the market for innovative solutions have prompted SKS to offer the Power Joint in different versions to meet the different customer requirements.
Power Clutch series:
The SKS precision standard
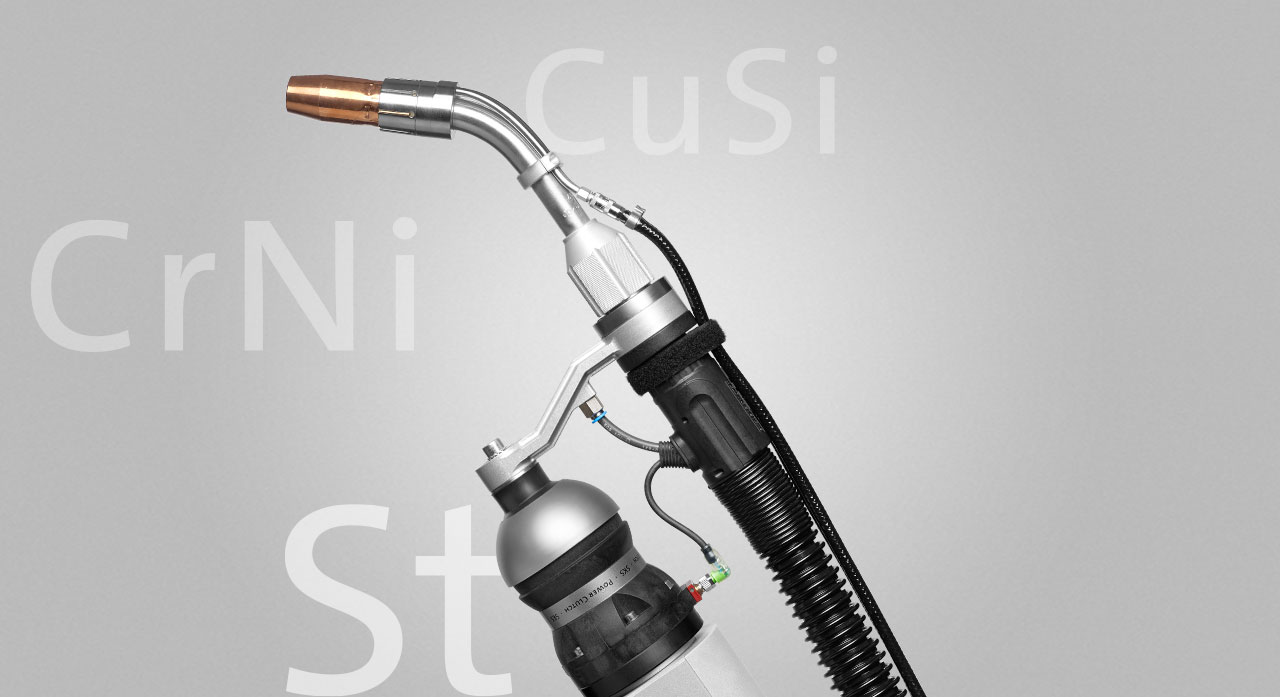
The welding torches of the Power Clutch series define the SKS precision standard for industrial robots with externally guided torch cables, supporting MIG/MAG, pulse welding processes and MIG brazing for all low- to high-alloy steels, aluminum as well as copper alloys and nickel-based materials. Because of the modular design of the Torch system, the Power Clutch is available in both air-cooled and water-cooled versions. By simply adding further parts, the torches of the Power Clutch series are easily expandable for any application and flexible in use.
Dual Wire 2.0:
High Performance Welding by SKS
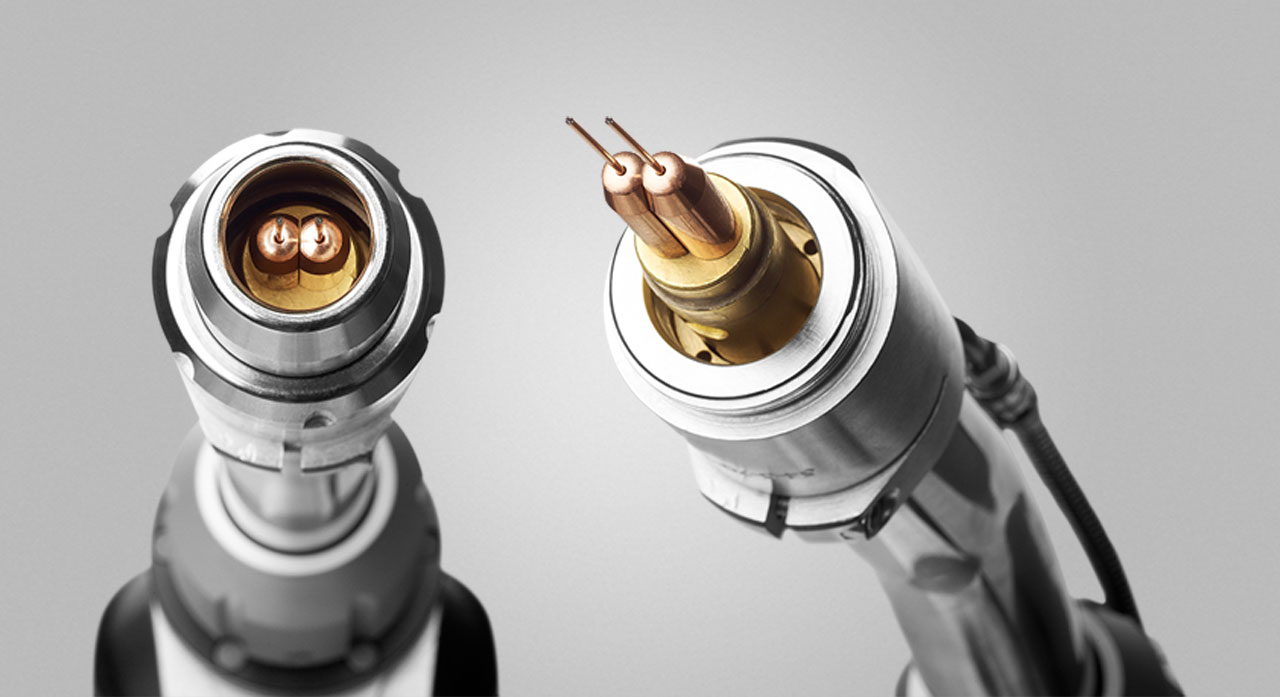
Dual-wire welding with the SKS Dual Wire 2.0 torch system. The Dual Wire 2.0 welding torch extends the SKS portfolio of appliances for fast welding with high deposition rates. The Dual Wire 2.0 has many features in common with our single-wire torches: The Power Clutch collision protection and the mechanical bayonet connection concept that allows the tool-free exchange of the torch neck – with an accuracy of ± 0.5 mm (Tool Center Point, TCP).
Wire Select 2.0:
Welding with automated wire change by SKS
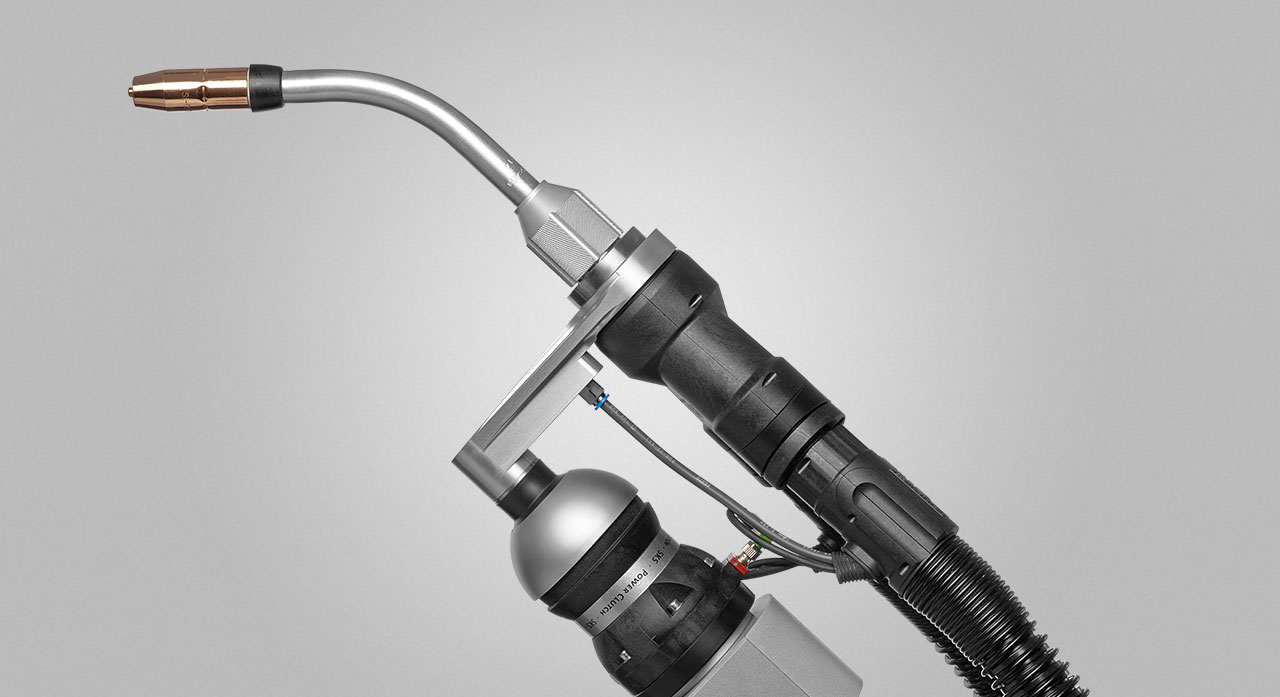
The Wire Select 2.0 welding torch allows welding with two different wires on the same workpiece – without the need to change the torch or supply lines. With only one power source, one controller, one torch, and two wire feeders, you are able to complete your welding task using two different weld fillers, two different gases, and different processes (e.g. Pulse welding and MIG brazing) in a single production unit. Long and inefficient changeover times required to change the weld filler are eliminated.
SPM (Special Purpose Machine):
For stationary applications without robot
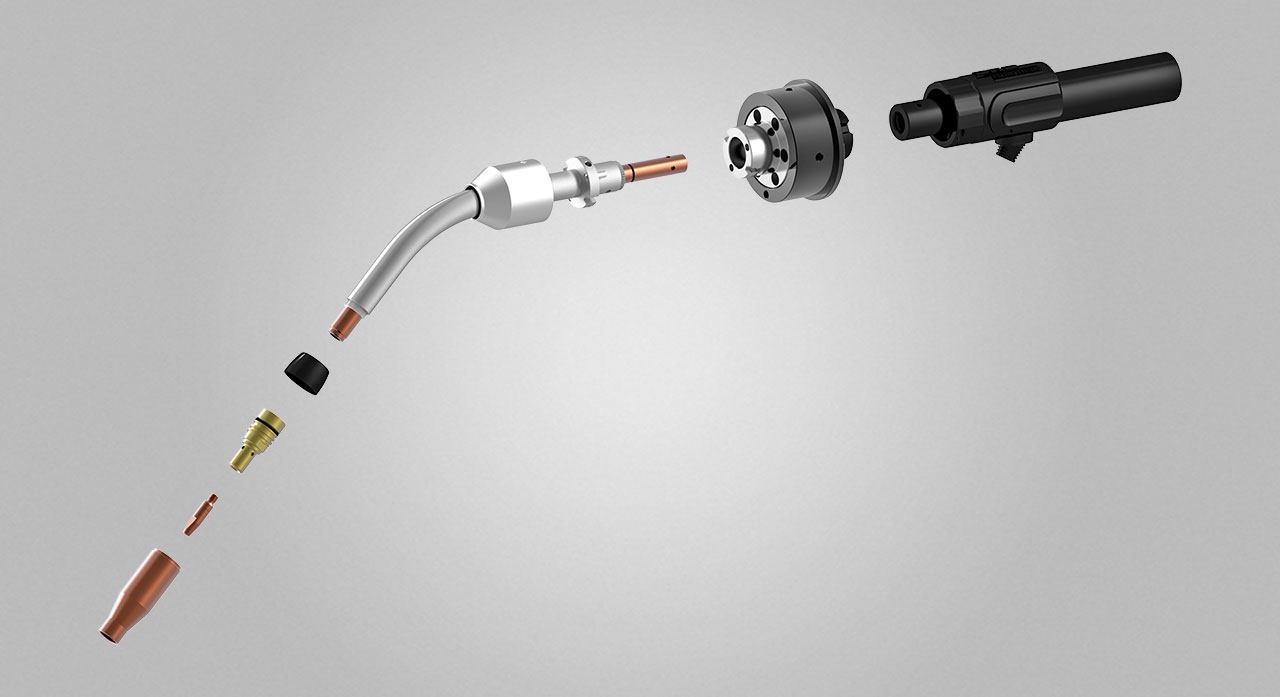
The SPM Weld Package is suitable for applications in which a robot is not required and a simple automatic welding machine performs the welding task. The SPM welding torch system is available in two versions (SPM and SPM Lite).
Semi-Automatic Machine (SAM) mobile/stationary:
Manual welding with robot precision
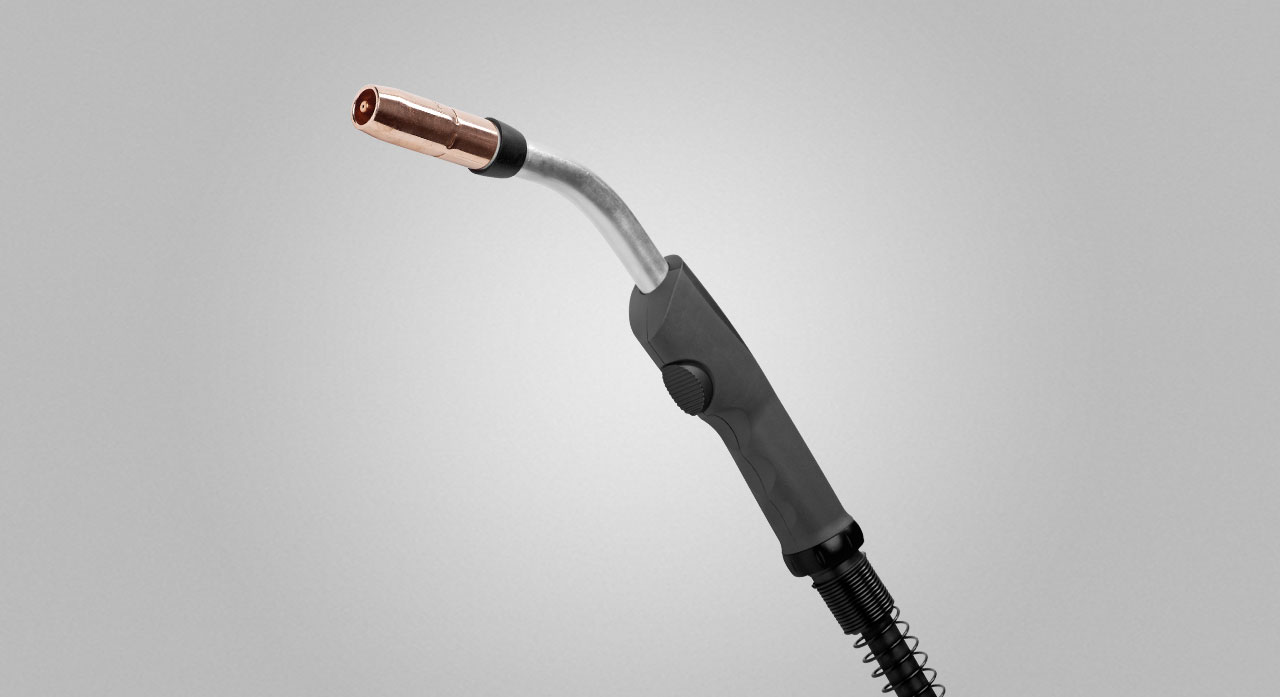
Modern MIG/MAG robot welding technology meets the highest quality requirements, which manual welding technology must also meet. The constant desire for complete automation is contrasted by technical feasibility and economic efficiency when it comes to complex component geometries. In some applications, it therefore makes sense – technically and economically – to use manual processes for the last welding steps. However, the same high quality is required here as in robotic welding.
To ensure the quality of robotic welding equipment is also available for manual welding technology, SKS has developed a special Weld Package and and implemented it with proven components from its robot applications. SKS offers two differently designed Weld Packages for mobile or stationary use.