microMIG Process:
Mechanical droplet detachment with intermediate pulses
Basically, the microMIG process can be divided into two phases. During the ("hot") pulse phase, the heat required to melt the base material is controlled by a rapid sequence of pulses to achieve the desired deposition rate. Due to the significant reduction of the applied arc energy during the second ("cold") phase, the short-circuit phase, the material can dissipate heat from the welding zone into more remote areas. In total, this leads to a significant reduction in the heat input.
During the hot phase, the wire is fed forward and a rapid sequence of pulses occurs. This heat input creates a weld pool on the base material, and with each pulse a droplet is transferred into the weld pool. Only the last pulse is used to create a molten drop at the end of the wire. This drop is immersed in the weld pool in the following cold phase, during which the current intensity is significantly reduced and the arc is extinguished when the wire is immersed in the weld pool. By reversing the wire feed direction, the last drop is mechanically detached and the arc is re-ignited. After reaching the set arc length, the wire feed direction is reversed again and the process is repeated with the next pulse series.
Special features – microMIG
- heat-reduced welding process
- better control of the heat input into the workpiece
- less workpiece distortion
- welding with low spatter and uniform penetration
- clean welding process – reduces maintenance efforts
- excellent gap bridging
- wider welds – larger process window in case of misalignment
- welding speed comparable with standard MIG/MAG processes
- very appealing weld appearance
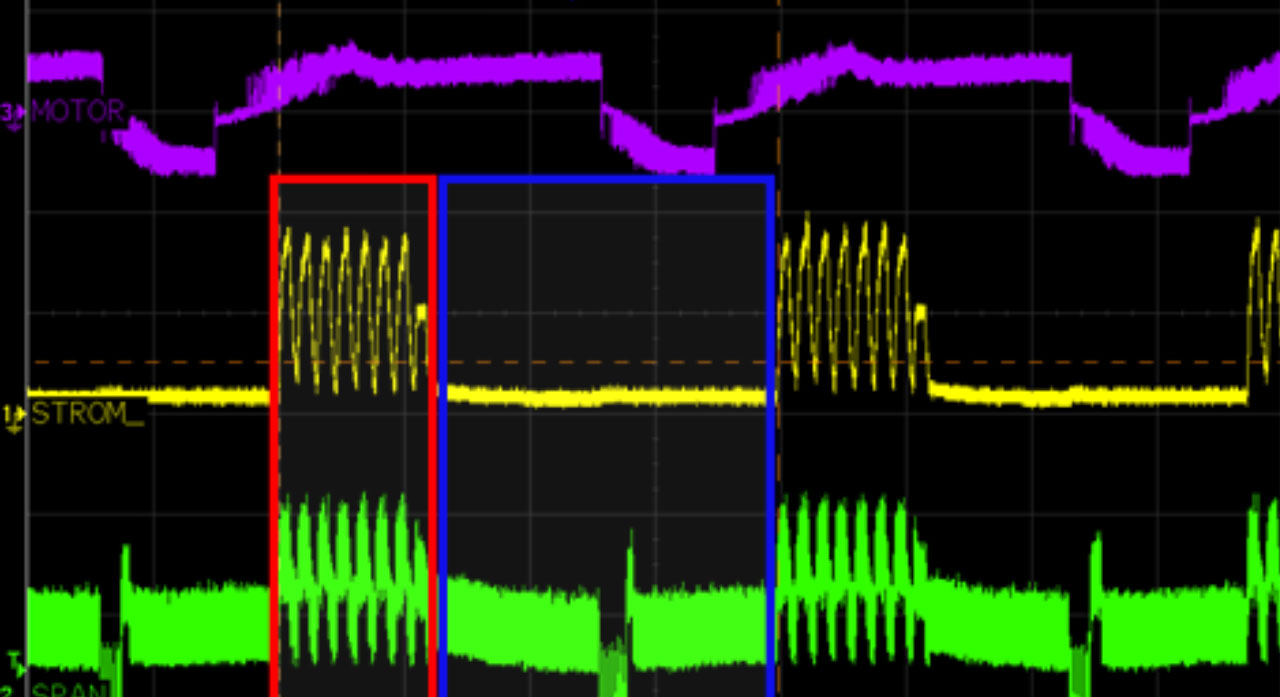
Highspeed video: SKS microMIG welding process
SKS Weld Packages
This might also interest you
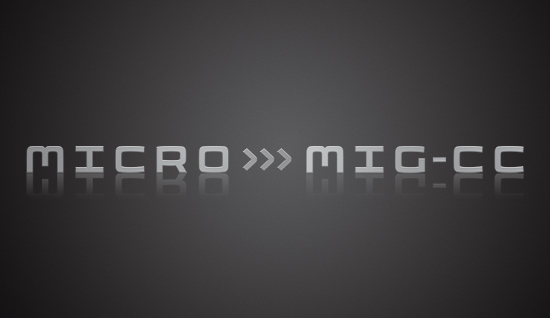
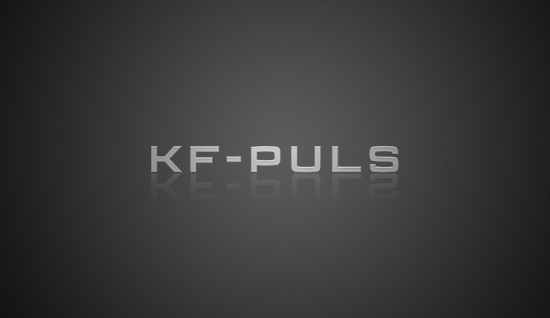
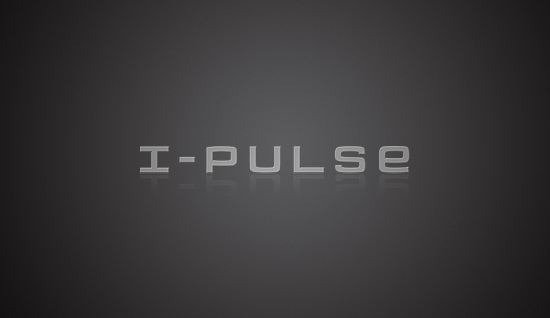
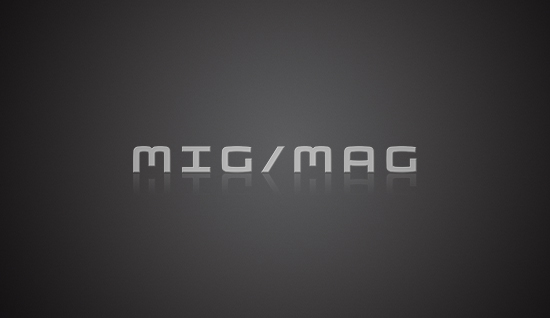