Torch System Equipment
SKS spare parts and wearing parts for welding torches
SKS torch systems are characterized by their highly modular design. In addition to savings in storage costs (as fewer components need to be stocked) installation and maintenance are simplified. The know-how used for each single component is mirrored within the complete single-wire torch line so that their benefits are included in all systems.
SKS torch necks are available in different lengths and geometries and can be used with all SKS single-wire torch systems. This provides for a high flexibility concerning the accessibility of the workpiece. Only system-related differences lead to changes to individual torch systems as, for example, in the case of process-arm robots with internally guided torch cables. Notwithstanding these system-related differences, the modular concept supporting the systems’ flexible use is always maintained.
Robot-specific flanges
The requirement for quick and easy mounting of torch systems to the various types of robots is met by SKS with a wide range of flanges. They provide for a precise connection between the robot wrist and the torch system. For robots with internally guided torch cable, complete mounting kits are available, consisting of a locating cover, a clamping sleeve, a sealing grommet, the robot-specific mounting flange, and all additionally required mounting materials
SKS collision protection for highest precision
In the event of a collision, the torch neck is deflected by up to 10°, protecting the welding torch and the robot from damage. When the preset switch-off point is reached, a switching contact signals the collision to the robot. A spring-based system returns the torch neck to its original position (TCP) with an accuracy of ± 0.2 mm.
Collision protection – special features
- based on the technology of the Power Joint
- consistently further developed
- Power Clutch and Power Clutch HD (with increased load capacity)
- also fixed (non-rotating) mounting possible (“PC replacement” / Power Joint Lite S / Frontpull 8i Lite) – support for robot collision detection
- reset accuracy +- 0.2 mm (at 400 mm)
Welding torch cable
SKS torch cables are made of highly flexible coaxial cable with 72 mm² conductor cross-section. The big cross-sectional area ensures a low electrical resistance to transmit as much power as possible to the process – leading to higher process stability. A shut-off line for connection to the collision protection system and a blow-out hose for subsequent blowing out of the gas nozzle with compressed air are optionally included in the torch cable. A corrugated protection tube with anti-kink springs on both sides ensures high stability of the external torch cables and thus leads to a longer service life. To ensure a predefined cable routing during different robot movements, the protection tubes are available in customized lengths matching the dimensions of each robot. Internally guided torch cables are designed for the specific arm length of the robot. All torch cables are equipped with power pin connection by default. Universal cables and other torch connections are available for adaptation to different welding systems.
Description of the SKS Power Pin
SKS Power Pin for the safe transmission of power and gas. The transmission of power is carried out via the whole surface of the Power Pin thereby reducing the contact resistance. Gas is guided inside of the Power Pin providing for a safe flow of gas.
Torch necks for highest dimensional accuracy
SKS torch necks are available in different geometries and lengths to match all single-wire torch systems. Besides their good accessibility, the torch necks feature a high material strength by design and air-cooled versions are capable to handle a maximum load of 420A at a duty cycle of 60%. While water-cooled torch necks are usually manufactured from thinner-walled materials and are thus easily deformable, SKS’ air-cooled torch necks are “rugged by design” and feature a high dimensional stability. This ensures that the TCP of ± 0.2 mm can be kept even when touched in an “ungentle” way.
In addition, SKS torch necks provide a large contact surface for low-resistance transmission of the current. A bayonet quick-lock connection system enables quick and reliable change cycles under adherence to a TCP of ± 0.2 mm.
For applications with higher duty cycles and aluminum applications, SKS‘ HQX series of torch necks is the right choice. A reinforced outer wall, as well as the approximately 80% increased amount of copper in the inner part, additionally increase the current transfer to the component as well as the heat dissipation of the front end.
For applications requiring a particularly high accessibility, SKS offers a special version of its torch neck (ZK version, maximum load: 250 A @ 60% duty cycle). This version requires a smaller insulator, a more compact retaining head and a shorter gas nozzle. Our standard contact tips can also be used with ZK applications.
- Integrated torch neck torsion protection implemented by means of offset, oppositely arranged dowel pins.
- Precise manufacturing of the individual components ensures the centering of the torch neck (± 0.2 mm @ TCP 400 mm). In addition, tool-free torch neck change is possible.
- The integrated wave spring guarantees constant contact pressure of the torch neck and makes sure that it stays locked in its end position.
Liners
Front load liners for torch systems
A reliable wire feeding system extends the service life and stabilizes the process. To this end, choosing the right wire core is an important factor. SKS wire cores are offered for steel/bronze and aluminum for different wire diameters: 0.8–1.6 mm (steel/bronze) and 1.0–1.6 mm (aluminum). This ensures that the harder steel/bronze wire and the softer aluminum wire can be reliably guided. Additionally, our wire cores are available in different lengths.
Front Load liners for the Power Joint and Power Clutch torch systems
The Power Joint torch system uses Front Load liners: The liner is loaded from the front. This only requires disassembling the wearing parts.
Liners for the Wire Select torch system
The Wire Select system uses three liners. Two of them are inserted into the Power cable from the side of the wire feeder and centered using an end sleeve, after the Power Pin cap has been removed. After opening the bayonet clamping cap without tools, the liner at the torch neck is inserted into the torch neck from the rear and screwed in place.
Liners for the Frontpull torch system
The Frontpull torch system uses two liners – one in the torch neck and another one that guides the wire from the Frontpull torch body to the Frontpull module. The front liner is inserted from the torch body to the torch neck, the second is inserted into the Power Cable from the side of the Frontpull module as with the Wire Select system.
Downloads
Retaining heads:
Perfect for fast gas nozzle replacement with absolutely secure fastening
Along with the contact tip, the retaining head is one of the most stressed parts in the entire welding system. Here, a long service life and precision centering of the contact tip are among the main criteria when it comes to producing perfect welding results. In order not to leave these points to chance, SKS manufactures all TCP-relevant wearing parts in-house. The production of wearing parts from the highest quality basic materials is a matter of course for us. SKS retaining heads are also available in different versions: in the Power Lock version and the newer Power Lock Plus version with trapezoidal thread. Adaptations of SKS wearing parts to individual applications are also available on request.
SKS Power Lock Plus retaining heads are screwed to the torch neck and serve to distribute gas and securely hold the contact tip and gas nozzle. Particularly in the case of wearing parts, the precision of the individual components is very important, as otherwise tolerances can add up unfavorably when these parts are changed. For this reason, SKS wearing parts are produced in-house. A trapezoidal thread ensures a secure fastening to the torch neck, and a conical surface tapered in the direction of the contact tip provides for an optimized transmission of power and heat.
Downloads
Contact tips
SKS contact tips are fastened to the retaining head via a high-precision thread. The conical design above the thread surface provides for enhanced heat dissipation, a higher TCP reproducibility and a better arc quality (based on the optimized power transmission / bigger transmission surface). Contact tips are available for wire diameters from 0.8 to 1.6 mm and in two different versions: for standard applications and for applications with high power ranges and/or long duty cycles. Just as our retaining heads, also out contact tips are produced in-house to ensure their consistently high quality: Made in Germany. Made for Robots.
Contact tip key
The contact tip key allows the quick change of the contact tip without removing the gas nozzle first. With this simple but useful tool, set-up times can be considerably reduced. Additionally, the contact tip key supports a defined fastening of the contact tip to the retaining head. With this tool, SKS contact tips for single-wire applications can be changed in a quick and reliable manner..
Programming tip
The programming tip is a useful aid for programming a robot to produce a weld joint with a constant free wire length. It is screwed to the retaining head and corresponds to the length of the contact tip plus the free wire length. Therefore, it is available for the common free wire lengths of 12, 15 and 20 mm. Programming tips make it easier to precisely program weld joints.
Multi-Tool
The SKS Multi-Tool is a universal tool for changing the torch neck wear parts and the wire cores in the torch system and torch neck. Markings for cutting welding wire to length (cutting the “stick-out”) and the wire core additionally facilitate the replacement of wearing parts and consumables.
Gas nozzles
Diverse applications impose different requirements on consumables. To meet these requirements, we offer different types of gas nozzles. Gas nozzles are available in both conical and bottle shapes. Each shape is available in three versions that differ in their positions in relation to the contact tip: 3 mm recessed; 3 mm protruding; flush with the contact tip. For applications in high power ranges or with long duty cycles, we also offer heavy-duty versions along with our standard gas nozzles. For components with restricted accessibility, gas nozzles of the ZK equipment series (ZK version, maximum load: up to 250A @ 60% duty cycle) are available. For torch necks of the HQX series, separate gas nozzles for steel/stainless steel applications and optimized gas nozzles for aluminum applications are available.
Downloads
Reamer blades
Reamer blades with ejection opening are available for all wear parts series. The opening ensures that the removed material is ejected safely for optimum support of the reaming process. The use of high-quality base material ensures maximum service life.
Downloads
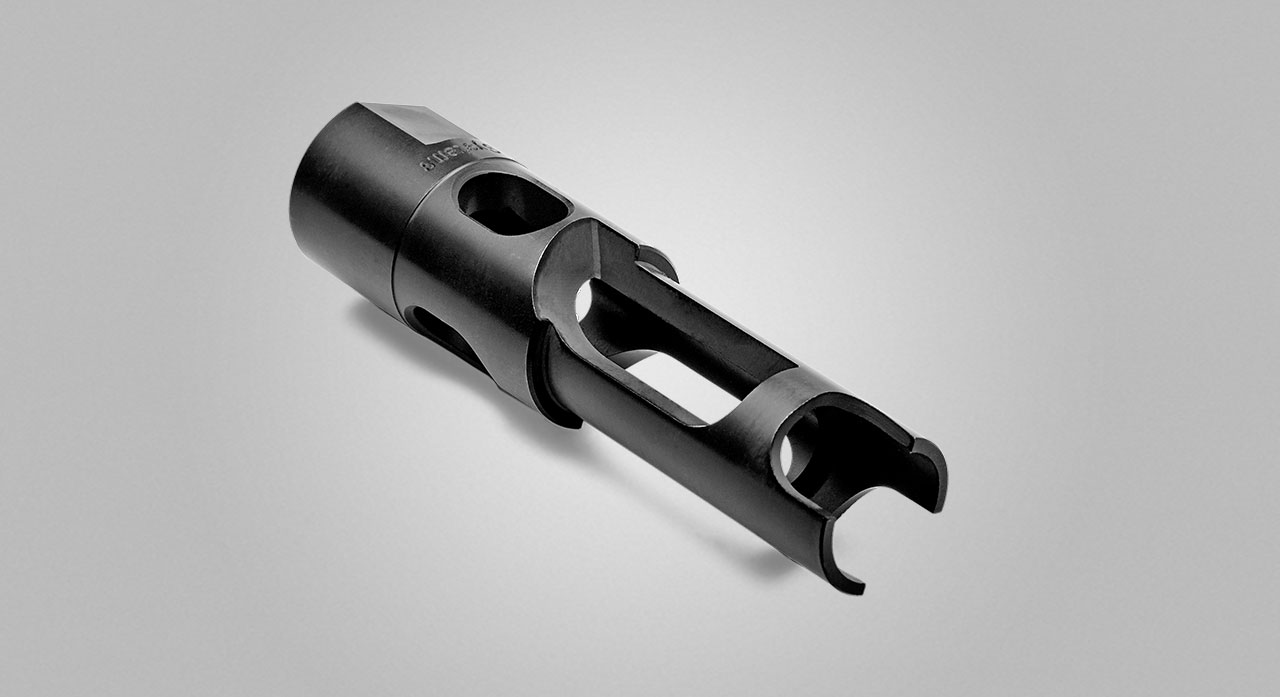
SKS Welding Systems Reamer Blade Power Lock Plus
Checking fixtures
The test fixture can be used to verify the TCP of welding torch systems (consisting of collision protection, torch arm and torch neck) or individual torch necks. The reproducibility of the TCP plays a critical role for automated arc welding. In order to comply with this criterion when changing the torch neck, the TCP can be checked for a preset checkpoint. The subsequent adjustment of torch necks was not considered in the manufacture of checking fixtures. Depending on the process speed, “slight” contacts during programming have only little impact on the system’s dimensional accuracy. However, if “violent” collisions should occur, it is recommended to verify the whole torch system and, if required, replace individual components. Torch necks are not considered wear parts at SKS. Because of our modular system concept and the possibility to combine our torch necks with different torch systems, a whole range of checking fixtures is required.
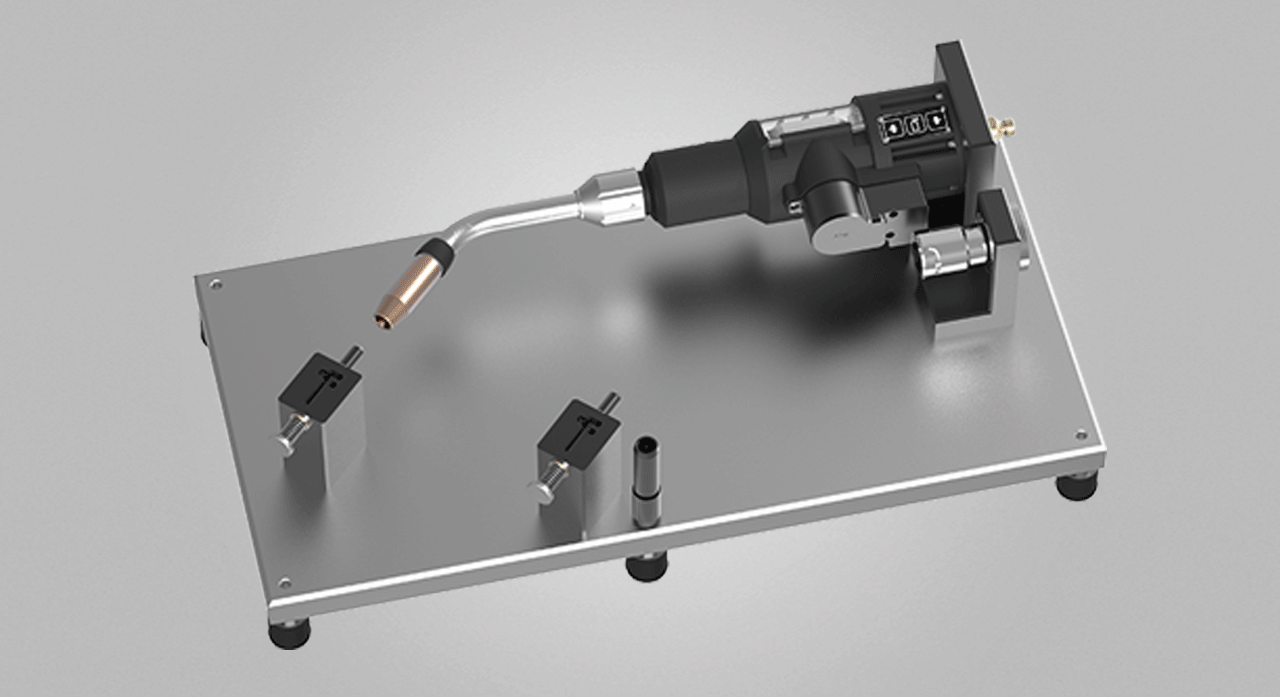