Welding Machine Equipment
SKS connection kits – equipment for perfect mounting on the robot: brackets and clamps
A system is only perfect when the highest possible attention is given to the details. To provide for compatibility with different robots, SKS invested a great amount of development time working on the required details: For welding robots by all manufacturers, SKS designed robot-specific solutions for the mounting of our torch systems and welding machine components.
SKS offers a large range of different flanges for the perfect mounting of SKS torch systems on the robot. Robust clip sets allow for proper mounting of the connection kits and cables to the robot arms. The part of SKS connection kits mounted directly to the robot can be disconnected from the motionless parts (connection to the power source) via a connection bracket, allowing for a quick and easy exchange of the robot-mounted part whenever maintenance works is required.
For all commonly used robot types, SKS offers mounting brackets for installation of the SKS wire feeders on the robots.
Wire guidance:
For the SKS Wire Feeder PF6
With the new wire guidance, the high efficiency of the whole system extends up to the drum.
- Wire Inlet Body for PF6 with Quick Connector
- Connection Nipple for FlexiGlide with tension spring
- Wire Guidance FlexiGlide
- Connection Nipple for FlexiGlide without tension spring
- Suspension for FlexiGlide
- Wall Duct for FlexiGlide
Download FlexiGlide
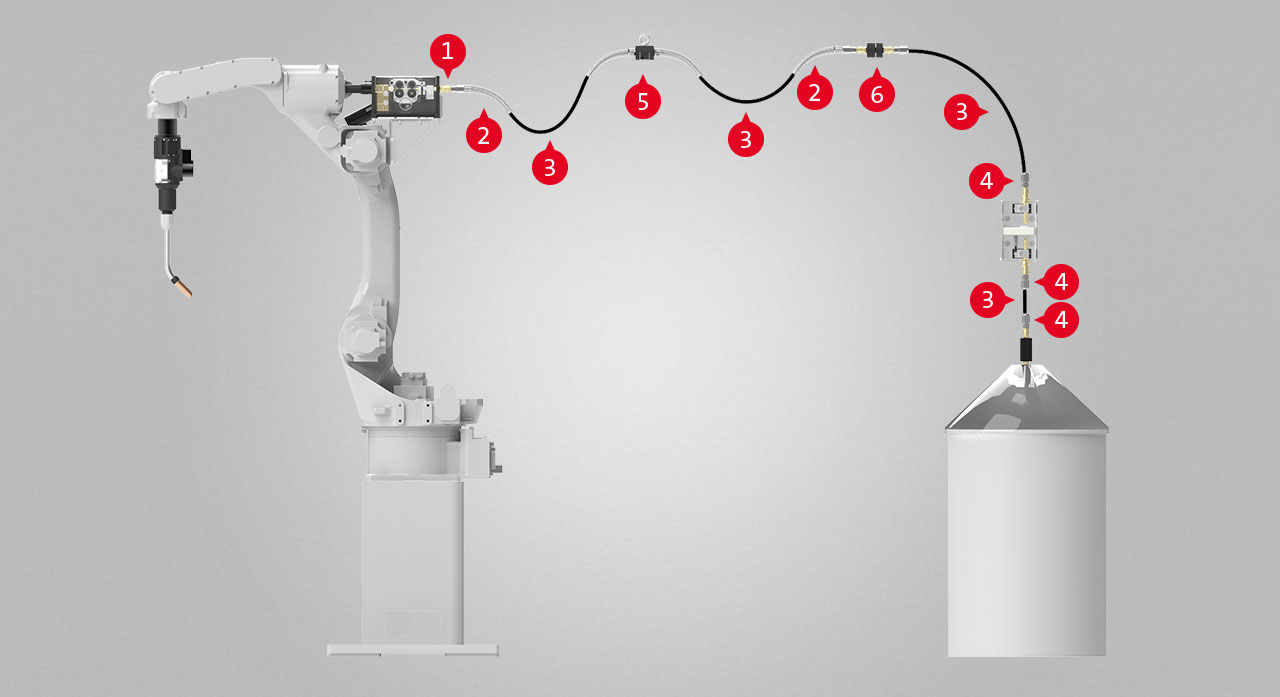
Overview FlexiGlide wire guidance
Benefits – SKS FlexiGlide wire guidance
Benefits – SKS FlexiGlide wire guidance
- Extraordinary good glide properties reduces motor load
- Minimized abrasive wear and reduced dirt in wire feeder and torch system
- Lightweight design and a high inherent stability for easy installation
- Length can be freely chosen by the customer
- Cost optimized exchange: only the FlexiGlide conduit must be changed, connectors are reuseable.
- Optimized materials for longer life and reduced downtimes
Water Module WM-01:
Water monitoring, Dual Wire for PF6
Ensuring heat dissipation is an essential factor for a high operating time of the welding system. The WM-01 water module, which can be easily integrated into new and existing welding systems, detects the water flow rate and sends a signal when it falls below the limit, that the weld system is not negatively affected and is quickly ready again. The integration is realized by means of common industrial connections.
Air-Blast Valve ABV-01:
For installation on wire feed console
The ABV-01 air-blast valve provides a controlled cleaning of the torch front end using compressed air. It can flexibly be mounted and is controlled via 24V DC.
Download Air-Blast Valve ABV-01
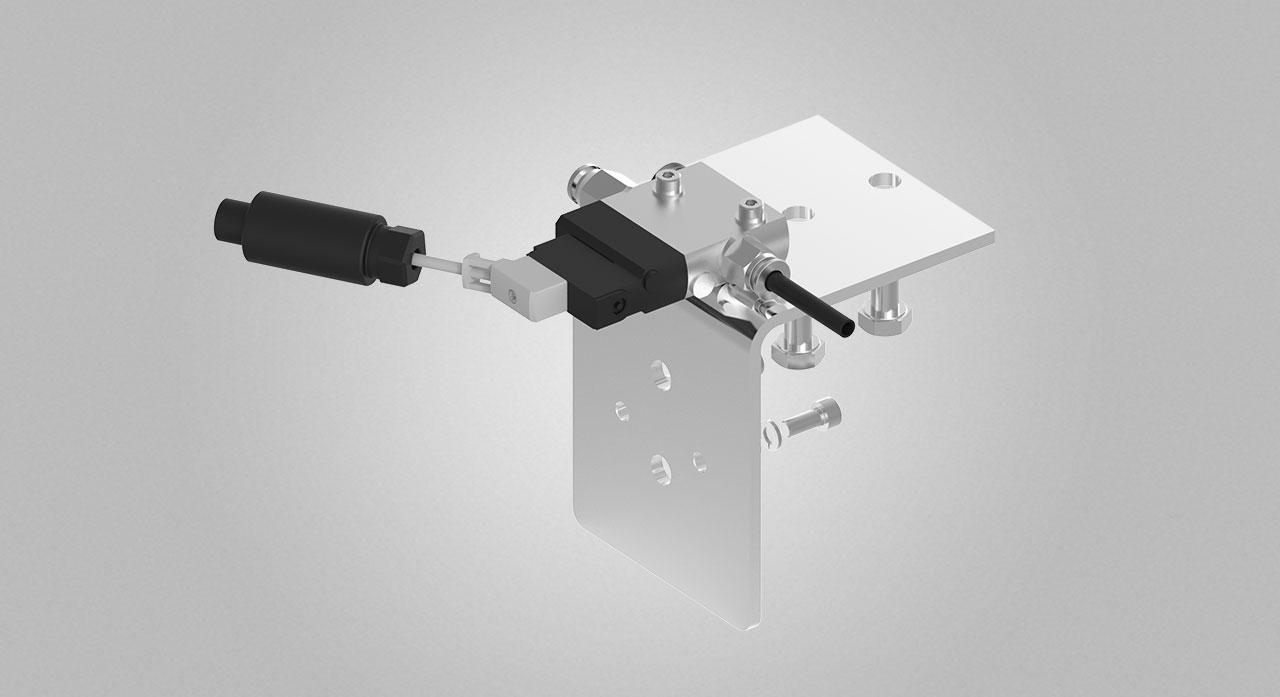
Shielding Gas Saver
Welding with MIG/MAG (GMAW), mostly single-stage pressure regulators with manometers or flowmeters are used. In the end of the welding process the solenoid valve of the welding system is closed. As a result, an overpressure in the gas feeding arouses between the welding machine and the pressure regulator. After restarting the welding process, the gas pressure is reduced with gas losses. By using the Shielding Gas Saver, the working pressure is reduced to a minimum. Tests with spot and tack welding showed cost savings of up to 50 %.
Comparison of gas flow rate from the pressure regulator at spot and tag welding with and without shielding gas saver The benefit of the Shielding Gas Saver is its pre-regulated working pressure of 1.2 bar (usually 4.5 bar). Therefore, the dynamic pressure is reduced, i.e. the Shielding Gas Saver provides benefits during ignitions. So, gas can efficiently be saved.
The Shielding Gas Saver ensures a constant gas flow during the welding task. The dynamic pressure within the cable bundle between welding machine and pressure regulator is reduced to a minimum. The Shielding Gas Saver can easily be used with pressure regulators at bottles or ring pipes, because the Shielding Gas Saver just reduces the pressure, not the flow speed. Normally there is no need for further adjusting.
Download Shielding Gas Saver
Gas Flow Sensor:
The next step to a more reliable process
The industrial proven Power Feeder PF6 has been advanced with an additional monitoring functionality: an integrated gas flow sensor. Especially with complex parts a fall of the required gas flow rate leads to high costs, since the welded part may be no longer usable, at best, it can only be "rescued" by a costly reworking. Therefore, the PF6 is now available in a version with an integrated gas flow sensor. The weld process controller displays the gas flow values, and can also be triggered to an alarm, in case of a non-defined gas flow rate.
Download Gas Flow Sensor
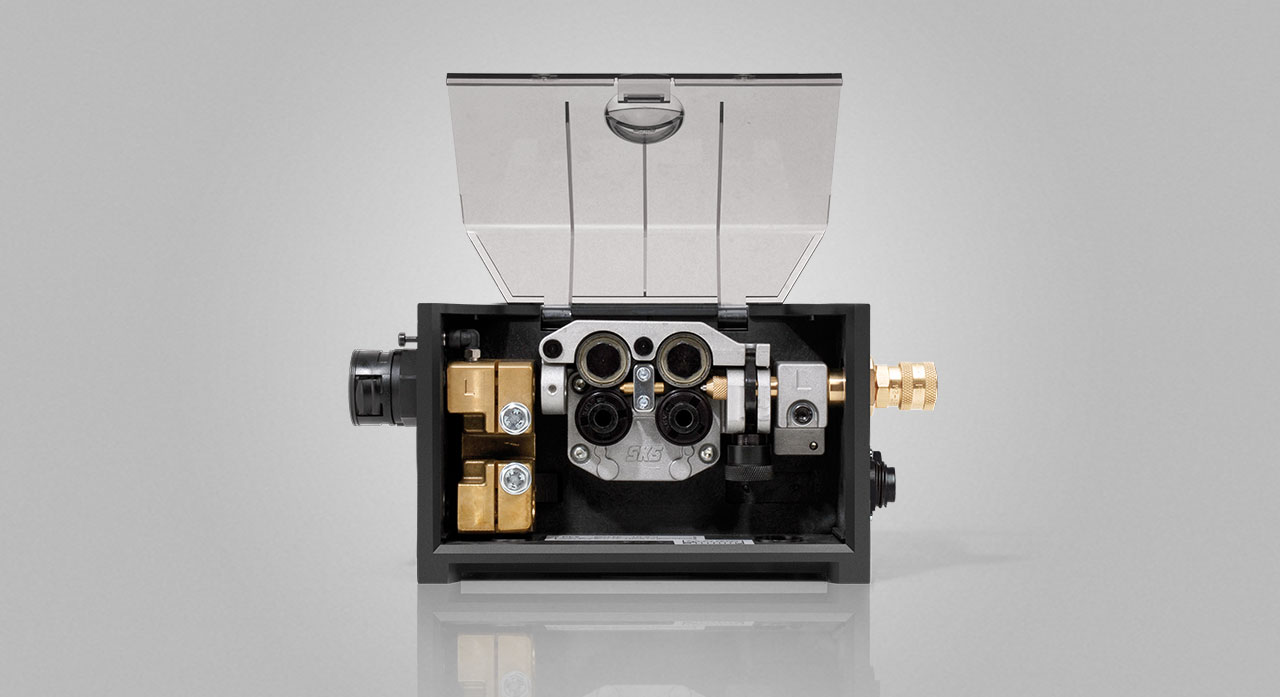
Ferrite Sensor FS-01
The Ferrite Sensor FS-01 offers the possibility to safely discern ferritic and nonferritic (e.g. austenitic) steel wire, because of their different magnetic attributes. The sensor is attached between the wire spool holder and wire feeder and the wire is lead through the hole of the FS-01. The sensor gives a signal output of +24V if the wire is ferritic. By assigning a type of wire (ferritic / non-ferritic) to each part in the PLC and connecting the signal output of the FS-01 to an input of the PLC, a wrong usage can be prevented. If ferritic wire is to be used, this allows you to check if a wire is inserted in addition.
Download Ferrite Sensor FS-01
Wire End Sensor WES-01
For installation on wire feed console (optional)
Minimizing error sources has a positive effect on the operating time of welding systems, and reduces defective workpieces as well as rework times. For this purpose, SKS offers simple solutions with great impact. For example, the wire end sensor WES-01 detects the end of the wire, the welding system is stopped automatically and the wire drum can be changed. To increase efficiency, welds that have been started can be finished using the remaining reserve of wire in the wire feeder. The wire end sensor WES-01 allows easy integration/updating of SKS wire feeding systems. The reliable detection of wire materials such as St, CrNi, Al for example, is done by means of an integrated proximity sensor.